Published on 2024-08-01
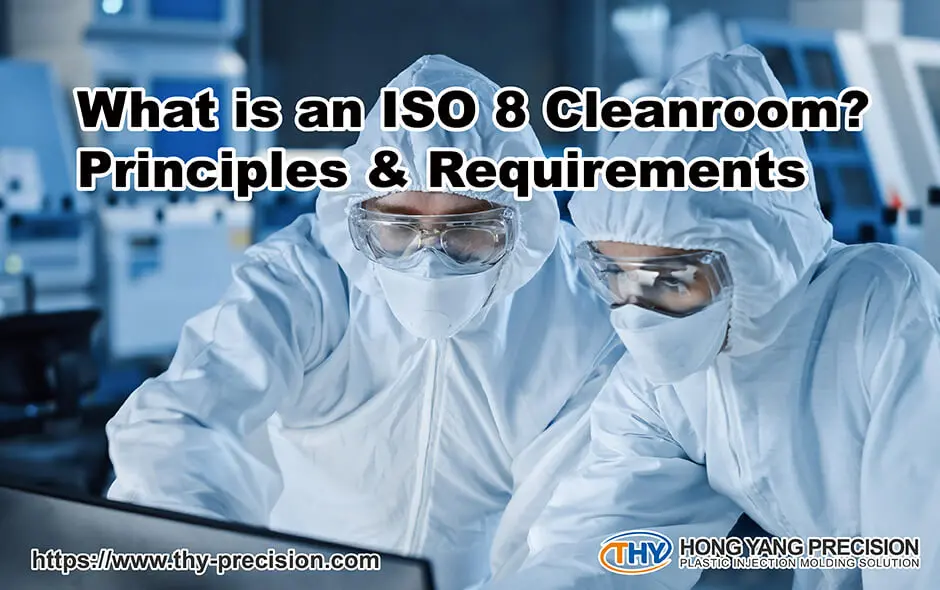
Even the smallest particle of dust can have a devastating impact when it comes to manufacturing sensitive medical devices and pharmaceuticals. That’s why these industries rely on cleanrooms.
Cleanrooms are designed to have a low level of airborne particles to protect products from contamination during the manufacturing and packaging process. They are certified to meet the standards of the International Organization for Standardization (ISO) 14644-1, which outlines classifications for cleanrooms ISO 1 to ISO 9.
Many manufacturers opt for an ISO 8 cleanroom, the second lowest classification, because it offers cleanliness and is cost-efficient.
So, what exactly defines an ISO 8 cleanroom?
Table of Contents
What is an ISO 8 Cleanroom?
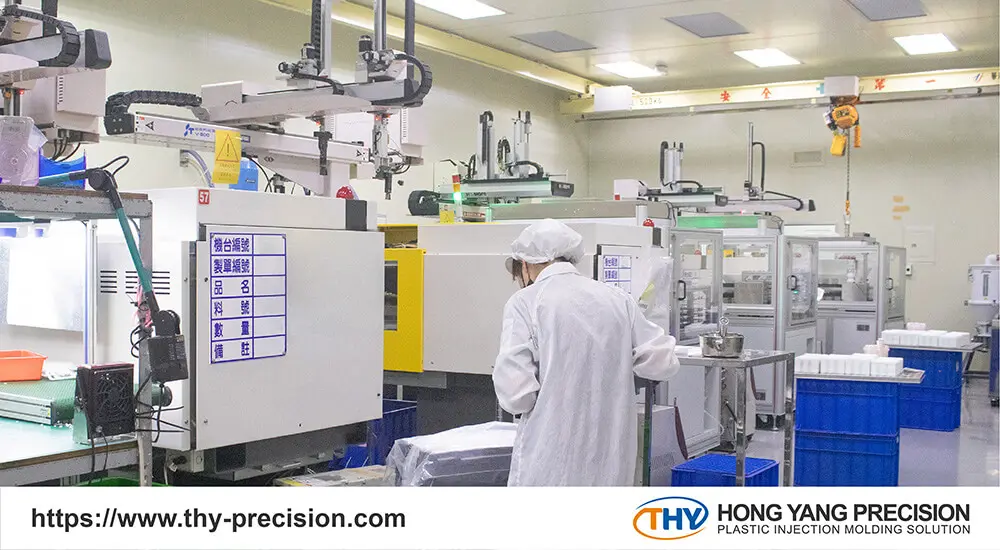
The ISO, an independent, non-governmental organization, acts as a global benchmark for cleanroom classifications across industries. It also establishes ISO standards for medical devices.
An ISO 8 cleanroom guarantees a controlled environment with a maximum allowable particle concentration of 3,520,000 particles per cubic meter that are 0.5 micrometers or larger.
High-efficiency particulate air (HEPA) filters, which remove at least 99.97% of airborne particles that are 0.3 micrometers or larger, maintain the air purity standards in ISO 8 Cleanrooms. This level of filtration ensures the quality and safety of products.
Common Applications of an ISO 8 Classroom
ISO 8 cleanrooms are used in many different industries to create a sterile environment, including:
- Pharmaceutical manufacturing: Preventing contamination during the production of sterile drugs, active pharmaceutical ingredients, and certain medical devices.
- Medical device manufacturing: Protecting medical implants, surgical instruments, and other sensitive devices during assembly and packaging.
- Electronics manufacturing: Ensuring the quality and reliability of semiconductors, microchips, and other electronic components.
- Optics manufacturing: Maintaining the precision and accuracy of lenses, mirrors, and other optical components.
- Food processing: Minimizing the risk of foodborne illness and cross-contamination.
- Aerospace manufacturing: Protecting aerospace components and instruments during assembly, testing, and calibration.
- Research laboratories: Providing a controlled environment for sensitive experiments and research, particularly in microbiology and biotechnology.
ISO 14644-1 Cleanroom Classifications
Here’s a table of the maximum number of particles allowed per cubic meter of air for each cleanroom classification, from the cleanest (ISO 1) to the least clean (ISO 9):
ISO Class | Maximum Particles per Cubic Meter (≥ 0.5µm) |
ISO 1 | 10 |
ISO 2 | 100 |
ISO 3 | 1,000 |
ISO 4 | 10,000 |
ISO 5 | 100,000 |
ISO 6 | 1,000,000 |
ISO 7 | 3,520,000 |
ISO 8 | 35,200,000 |
ISO 9 | Not defined (similar to ambient air) |
ISO 8 Cleanroom v.s. Federal Standard 209E
Before the global adoption of ISO 14644-1, the United States used Federal Standard 209E to classify cleanrooms. This standard is similar to ISO 14644-1, but uses different terminology and measurements.
In 2001, ISO 14644-1 officially replaced Federal Standard 209E to align with international practices for easier global trade and collaboration.
ISO Class | Federal Standard 209E (Equivalent at 0.5 microns) | Maximum Particles per Cubic Meter (≥ 0.5µm) |
ISO 1 | Class M1 | 10 |
ISO 2 | Class M2 | 100 |
ISO 3 | Class M3 | 1,000 |
ISO 4 | Class M4 | 10,000 |
ISO 5 | Class M5 | 100,000 |
ISO 6 | Class M6 | 1,000,000 |
ISO 7 | Class M7 | 3,520,000 |
ISO 8 | Class 100K | 35,200,000 |
ISO 9 | Not Defined (Similar to Ambient Air) | Not Defined |
Key ISO 8 Cleanroom Environmental Parameters to Control
These environmental parameters need to be controlled in order to ensure the level of cleanliness in ISO 8 cleanrooms:
1. HEPA Filtration
HEPA filters need to show a minimum efficiency of 99.97% at capturing particles 0.3 microns or larger in size. Regular testing and replacing HEPA filters help maintain their performance.
2. Air Changes Per Hour (ACH)
This refers to the number of times the air in a cleanroom is replaced with filtered air. For ISO 8 cleanrooms, a minimum of 20 air changes per hour is recommended to effectively dilute and remove airborne contaminants.
3. Airflow Patterns
ISO 8 cleanrooms use non-unidirectional or mixed airflow patterns. Low wall air returns directs contaminants away from work areas and towards the filters.
4. Air Pressure Management
By keeping a higher pressure inside the cleanroom than outside, unfiltered air can flow outwards when doors are opened.
5. Temperature and Humidity Control
Stable temperature and humidity levels ensure product stability and prevent microorganisms from growing. The temperature should typically stay between 64°F to 72°F, with a 40% and 60% humidity level.
6. Static Control Measures
Static electricity can attract and hold unwanted particles. Anti-static flooring, ionizers, and grounding straps mitigate the risk in ISO 8 cleanrooms, especially in electronics manufacturing.
7. Lighting and Noise Levels
Lighting and noise can severely disrupt manufacturing processes. Cleanroom lighting should be bright, glare-free, and energy-efficient. Noise levels should also be minimized.
8. Personnel Control
People are actually the biggest source of contamination in cleanrooms. Limiting the number of personnel inside, enforcing strict gowning protocols, and providing training on cleanroom practices are key to maintaining an effective cleanroom.
Types of ISO 8 Cleanroom
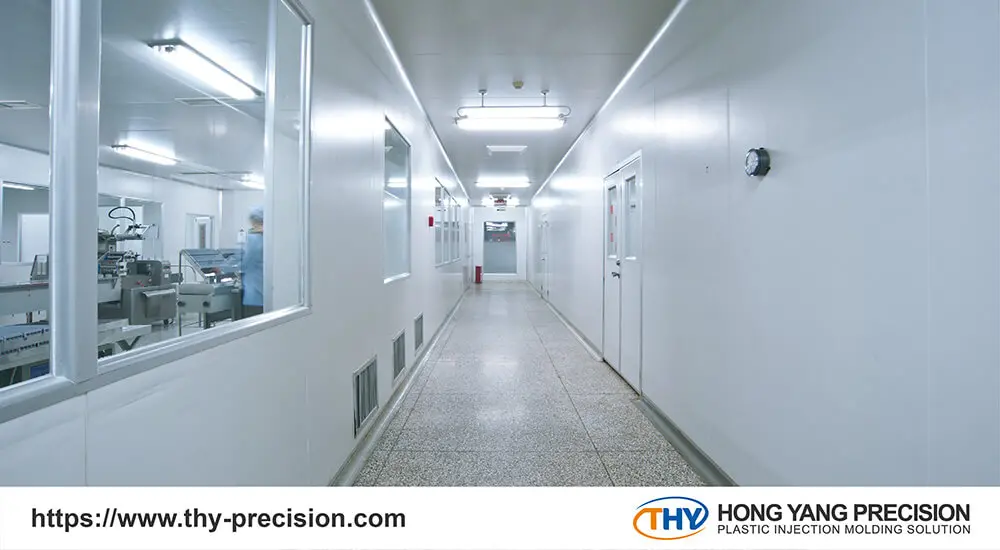
Depending on your application, space, and budget, there are three main types of ISO 8 cleanrooms to choose from:
● Modular Cleanrooms
Modular cleanrooms are a popular option because of their flexibility and cost-effectiveness. They are built with prefabricated panels and easily-assemblable components so they can be installed, expanded, or reconfigured with ease.
They’re great for manufacturers that need an adaptable and affordable cleanroom solution, particularly those with changing needs or temporary installations. The pharmaceutical and medical industries often use modular cleanrooms.
● Stick-Built Cleanrooms
Stick-built cleanrooms are a more permanent solution for larger facilities. They are built on-site using traditional materials like drywall, steel studs, and epoxy paint.
Large facilities, such as those in the semiconductor and aerospace industries, prefer this type of cleanroom because they can customize designs to fit their needs. However, stick-built cleanrooms are more expensive and time-consuming to build.
● Softwall Cleanrooms
Softwall cleanrooms use transparent vinyl curtains or panels to create a controlled environment. Their lightweight and flexible construction makes them a budget-friendly and portable option.
Applications that need frequent access and visibility, like food packaging lines, use softwall cleanrooms to quickly establish clean zones without disrupting workflow. Yet, because of their structure, there’s a higher risk of air leakage and contamination.
The Basic ISO 8 Cleanroom Gowning Procedures
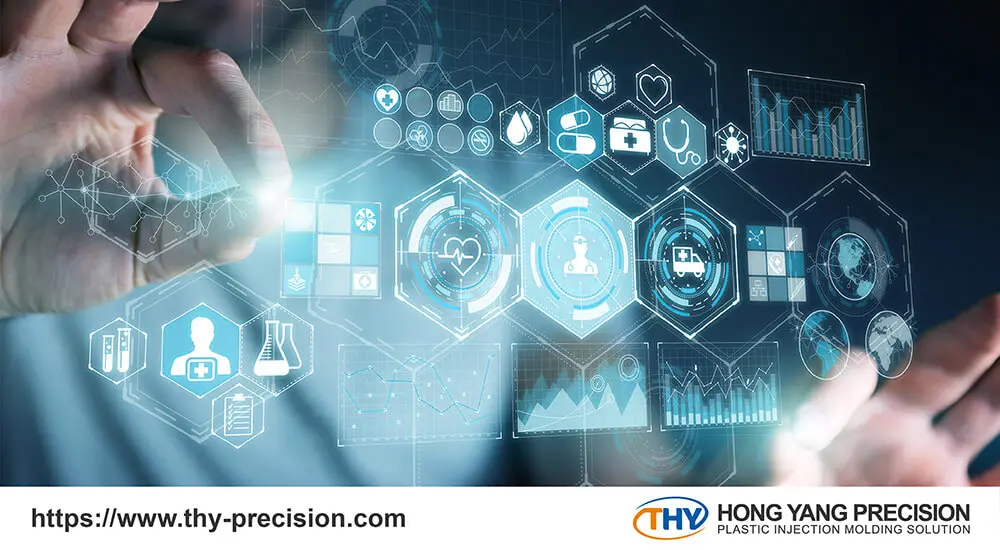
Skin flakes, hair, and clothing fibers can all compromise product quality and safety. Proper gowning procedures prevent contamination:
● Shoe Covers
Anyone entering an ISO 8 cleanroom must put on non-shedding shoe covers to prevent dirt and debris from being tracked inside.
● Head Coverings
Hair is a huge contamination source in cleanrooms. Personnel should wear a lint-free hairnet or a hood to cover their hair completely.
● Jackets or Coveralls
Jackets or coveralls cover regular clothing to stop lint, dust, and dander from entering the cleanroom.
● Gown Rooms and Airlocks
Gowning procedures are often done in a separate gown room or airlock. These areas are buffer zones between the outside environment and the cleanroom.
It’s also important to follow a specific gowning order to prevent cross-contamination. This ensures that cleaner items are not contaminated by dirtier ones.
● Others
Some cleanroom protocols require personnel to wear gloves to prevent oil transfers from the hand to products. Face masks are sometimes required to prevent saliva and respiratory droplets.
Cleanroom Solutions for Medical Devices: THY Precision Leads the Way
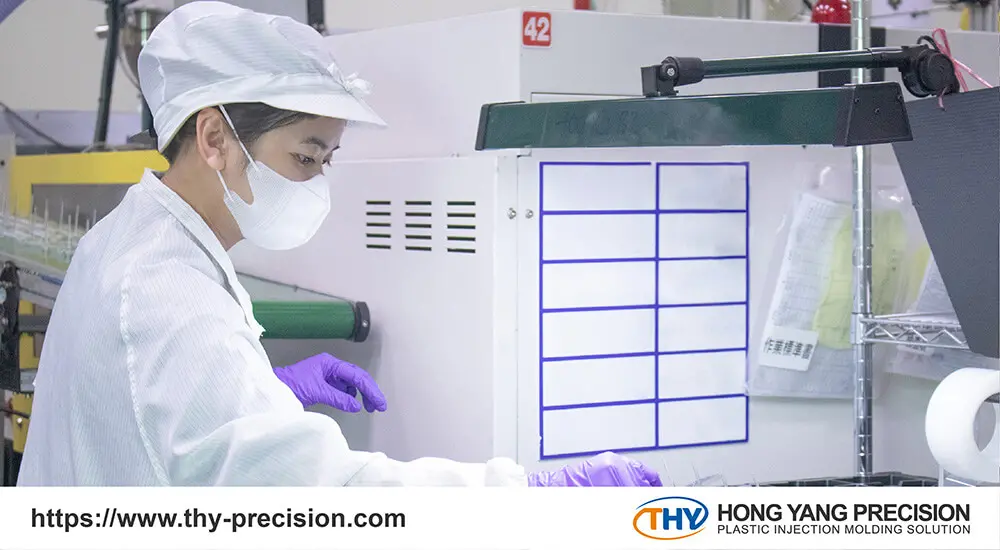
THY Precision understands your need for pristine and reliable cleanrooms. Our state-of-the-art facilities include a 13,000 sq. ft. ISO 8 cleanroom dedicated for injection molding, a 7,500 sq. ft. ISO 7 cleanroom assembly line, and a 54,000 sq. ft. climate-controlled injection molding area.
We ensure that every step of the manufacturing process is precise, accurate, and consistent. Our ISO 13485 certification also reflects our commitment to the highest quality management standards for medical devices.
Whether you need expert assistance with medical device manufacturing or cleanroom services, THY Precision is here for you — Contact us today.
Related articles:
Precision Injection Molding Basics and Design Considerations
Essential Design Guidelines for Precision Injection Molding