Published on 2024-09-05
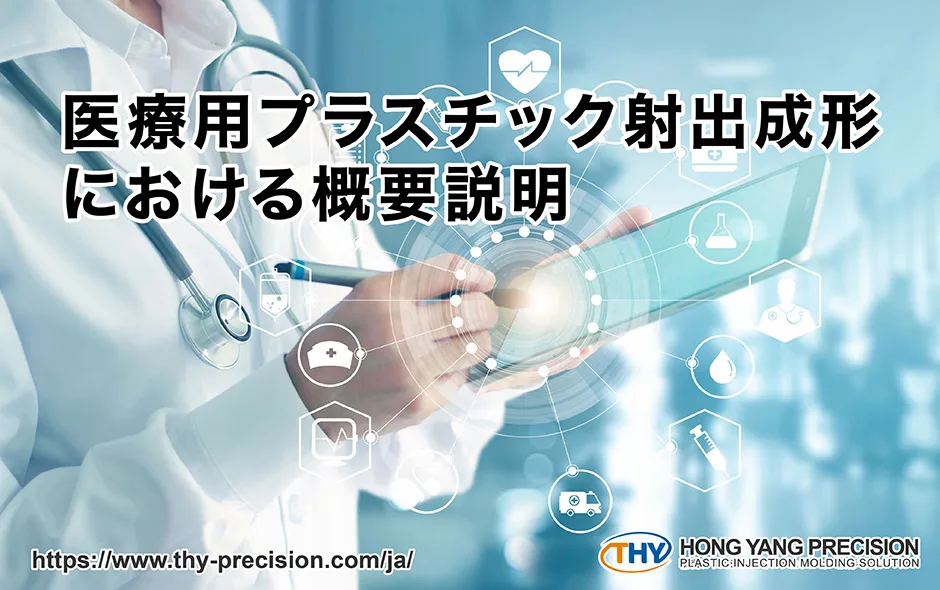
多くの医療用品の部品はプラスチック射出成形によって製造されています。この方法は、精密で高品質な部品を大量生産できるだけでなく、ISO規格との適合性も高めることができます。 一般的に、医療用のプラスチック射出成形はISO 8クリーンルーム環境で行われ、製品が厳しい衛生と安全基準を満たすよう確保されています。
本記事では、医療業界でのプラスチック射出成形の活用について、主要材料、実践的な技術、そして製造業者や医療提供者にもたらす利点に焦点を当てて解説します。
Table of Contents
医療用プラスチック射出成形で使用される主な材料
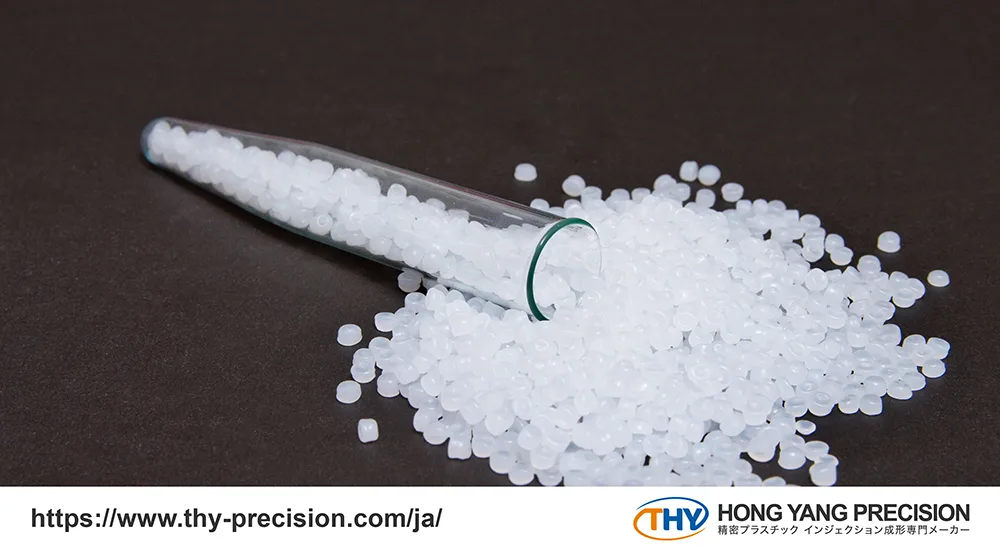
医療用射出成形では、医療グレードの樹脂を加熱して溶融状態にします。 樹脂を選択する際には、生体適合性、耐久性、その他の機械的特性を考慮する必要があります。
以下は、医療用プラスチック射出成形でよく使用される医療グレードのプラスチックのリストです:
● ポリプロピレン(PP)
ポリプロピレンは射出成形で最も広く使用される樹脂であり、例えば、眼疾患治療に用いられる眼内レンズ(IOL)など、精密でサイズが特定された医療部品を製造する際に使用されています。
医療グレードのPPは、注射器、コネクター、インプラントなど、幅広い医療用品や医療関連部品の効率的な大量生産を可能にします。 また、その強度、耐衝撃性、放射線耐性により、医療製品の部品として信頼性の高い素材となります。
● ポリエチレン(PE)
ポリエチレンには、低密度ポリエチレン(LDPE)と高密度ポリエチレン(HDPE)など、さまざまな形式があります。 LDPEは結晶度が低いため柔軟性が高く、一方HDPEは剛性と強度が高いという特徴があります。
PEは、関節プロテーゼ、チューブ、コンテナなどの耐久性のある生体適合部品の製造に一般的に使用されます。 その軽量性と化学的耐性により、滅菌や過酷な条件に耐える必要がある医療用品に適しています。
● ポリカーボネート(PC)
ポリカーボネートは光学的透明性と耐衝撃性で知られており、透明性と耐久性が求められる用途に最適です。 また、軽量なガラス代替品としても利用され、光学的透明性や耐久性が求められる医療用品に適しています。
射出成形で光学レンズを製造する際の考慮事項については、こちらの記事をご覧ください:
光学レンズ製造における射出成形の役割
医療用プラスチック射出成形でよく使用される技法
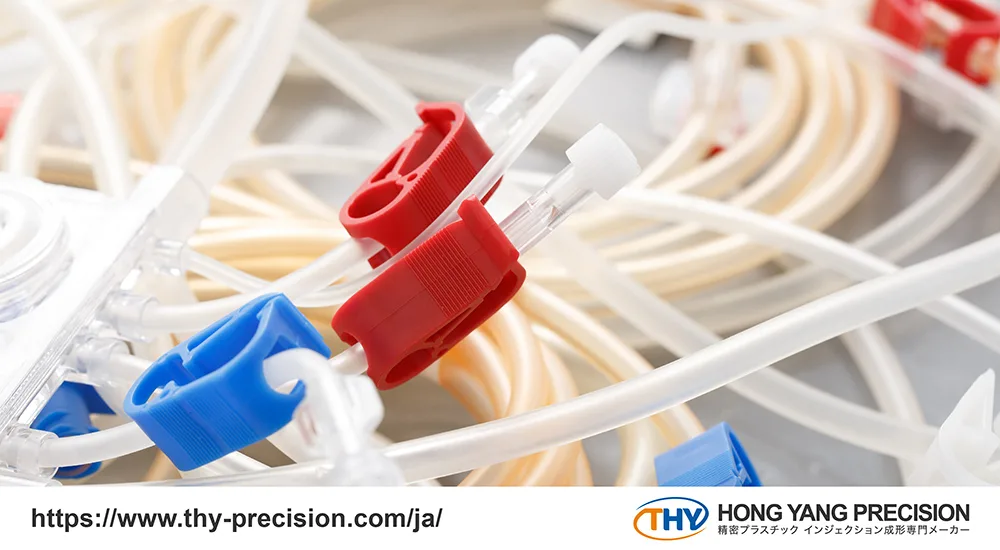
医療用品や医療機器の部品製造でよく使用されているプラスチック射出成形技法の 1 つに、薄肉成形があります。
薄肉成形は、壁厚が1mm未満の部品に適用される高精度な射出成形技術で、大量生産においてコスト効率を高めます。 このプロセスでは、材料が固まる前に型を適切に埋めるために、高い圧力と高速な成形が必要です。
例えば、標準的な壁厚の部品が2秒で成形される場合、壁厚が25%薄くなると1秒で成形する必要があります。
部品の射出を容易にするためには、適切なゲート設計が重要です。この技術は、小型の医療用品エンクロージャーの製造に頻繁に利用されます。
医療用品業界で使用される重要な検証プロセス:IQ、OQ、PQ
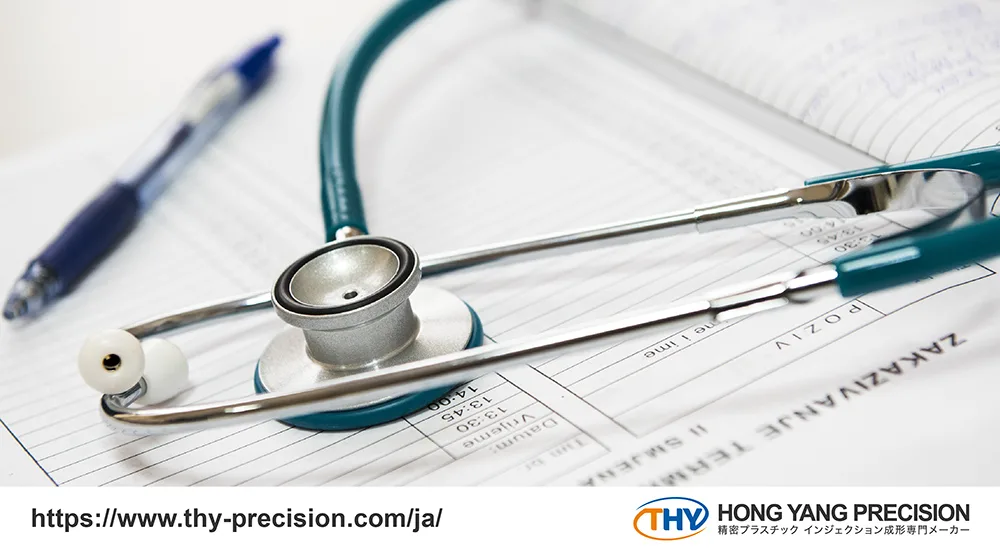
医療用品において、品質と安定性は極めて重要です。わずかな欠陥でも重大な影響を与える可能性があるためです。 射出成形の文脈では、特に薄肉射出成形のような繊細な部品において、厳格な品質保証(QA)が各段階で実施されるべきです。
バリデーションの主な3つの段階、すなわち設置適格性評価(IQ)、運転適格性評価(OQ)、および性能適格性評価(PQ)は、医療業界で広く使用されています。 これらの段階は総称して「3Qプロセス」と呼ばれ、射出成形プロセスが医療用品に求められる厳格な品質基準を満たす部品を一貫して製造できることを保証します。
● 設置適格性(IQ)
IQ(設置適格性評価)は、生産、測定、および試験プロセスで使用されるすべての部品が適切に設置、維持、校正されていることを確認します。 初期設置設定を文書化することは、プロセスの逸脱や部品の不安定性の根本原因を特定するために重要です。
● 運転適格性評価(OQ)
OQ(運転適格性評価)は、製品やプロセスの主要な性能要素が要求される仕様を満たしていることを確認します。 このバリデーションでは、分析手法や工学的研究を通じて、さまざまなプロセスパラメータに適切な運転限界を設定し、プロセスが一貫して許容範囲内の部品を製造できることを保証します。
● 性能適格性評価(PQ)
PQ(性能適格性評価)は、製造プロセスが安定しており、顧客の期待を満たす部品を生産できる能力を示します。 PQでは通常、定義されたプロセスを3回の独立した生産実行でテストし、実際の生産条件をシミュレーションして一貫した品質を確保します。
医療用プラスチック射出成形の利点
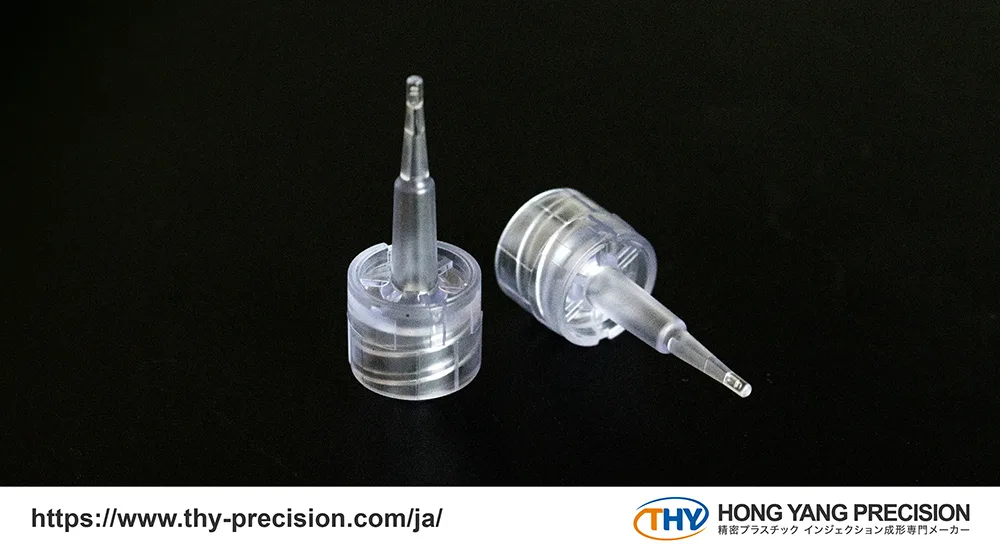
● 高い生産量と低いコスト
医療用のプラスチック射出成形は、大量生産において非常にコスト効率が高い方法です。 初期の金型製作には多額の費用がかかるものの、生産量が増えるにつれて部品1つあたりのコストは大幅に低下します。 さらに、このプロセスの自動化と高精度により、労働コストが削減され、各部品が効率的に製造されることが保証されます。
● 設計と製造の柔軟性
射出成形は、複雑な設計と精密な製造を可能にします。 ±0.1mm程度の狭い公差範囲(一般的な範囲)や、±0.005mmという高精度で複雑な部品を製造することができます。 この利点は、わずかな偏差でも性能や安全性に影響を与える医療用品にとって非常に重要です。
● 多様な医療グレード材料の利用可能性
射出成形プロセスは、多様な医療グレードの材料に対応しており、さまざまな業界基準や要件を満たす柔軟性を提供します。 この豊富な材料選択肢には、PP(ポリプロピレン)、PE(ポリエチレン)、PC(ポリカーボネート)、シリコンなどが含まれ、それぞれ異なる医療用途に必要な強度、耐久性、生体適合性を備えています。
適切な医療用射出成形パートナーの選び方
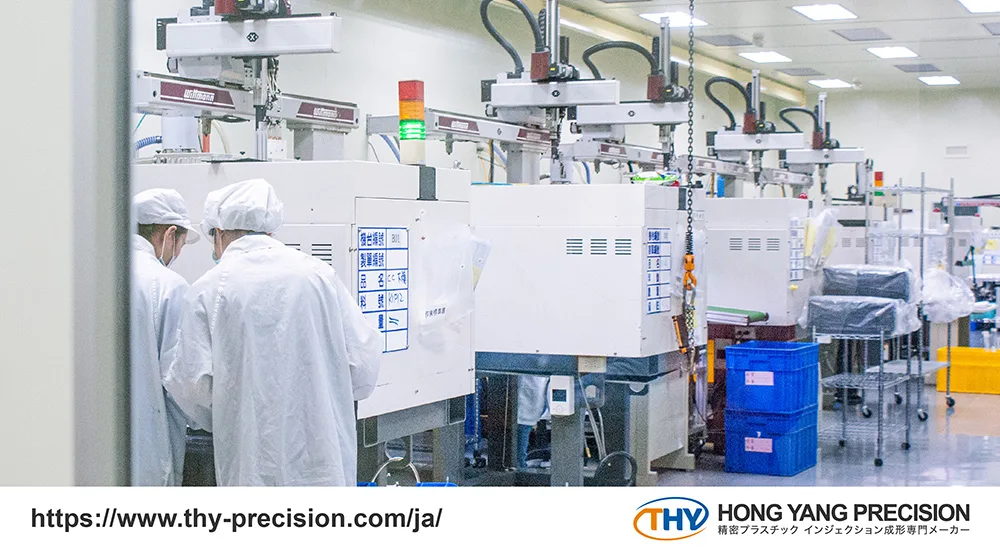
医療用プラスチック射出成形の適切なパートナーを選ぶ際に評価すべき重要な質問は以下の通りです:
- その会社は医療用射出成形にどのくらいの期間関わってきたか?
- これまでにどのような医療用品、医療関連製品を製造してきたか?
- 会社は医療関連部品の製造に関するFDA規制やISO規格に精通していますか?
- ISO Class 7およびClass 8のクリーンルーム環境に関する認証のがありますか?
- どのような射出成形機や技術を使用していますか?
- リアルタイムの監視と品質管理を提供していますか?
THY精密工業では、熟練したエンジニアがデザインの改善や部品に適した材料の選定をサポートしております。
当社は、30トンから300トンのプレス機を80台以上保有しており、毎月数百万個の部品を生産し、リアルタイムで品質監視を行っています。 当施設には射出成形用のISO Class 8クリーンルームと、組立用のISO Class 7クリーンルームがあり、生産および包装のための防塵された汚染のない環境を構築しています。 当施設には射出成形用のISO Class 8クリーンルームと、組立用のISO Class 7クリーンルームがあり、生産および包装のための防塵された汚染のない環境を構築しています。
一部の医療用品には滅菌サービスが必要です。THY精密工業では、EO(エチレンオキサイド)およびガンマ滅菌も提供しており、細菌、ウイルス、真菌による感染症のリスクから何百万もの患者を守るお手伝いをしています。
当社は、以下のようなさまざまなクラスIIおよびクラスIIIの医療用品の製造に経験があります:
- 医療用フィルターおよびインプラント部品:チャンバーフィルター、透析器フィルターなど
- 静脈注射および輸液部品:ポンプコネクター、静脈注射ドリップ部品、バクテリアフィルターなど
- 医療および実験室用消耗品:血液バッグ用プラスチック部品、ビーカー、ペトリ皿、実験室用容器、IOLアプリケーション用注射器など
プロジェクトにどのようにお手伝いできるかについての詳細は、お問い合わせいただき、THY精密工業がどのように医療用品プラスチック射出成形の要件をサポートできるかをぜひお問い合わせください。