Published on 2024-05-21
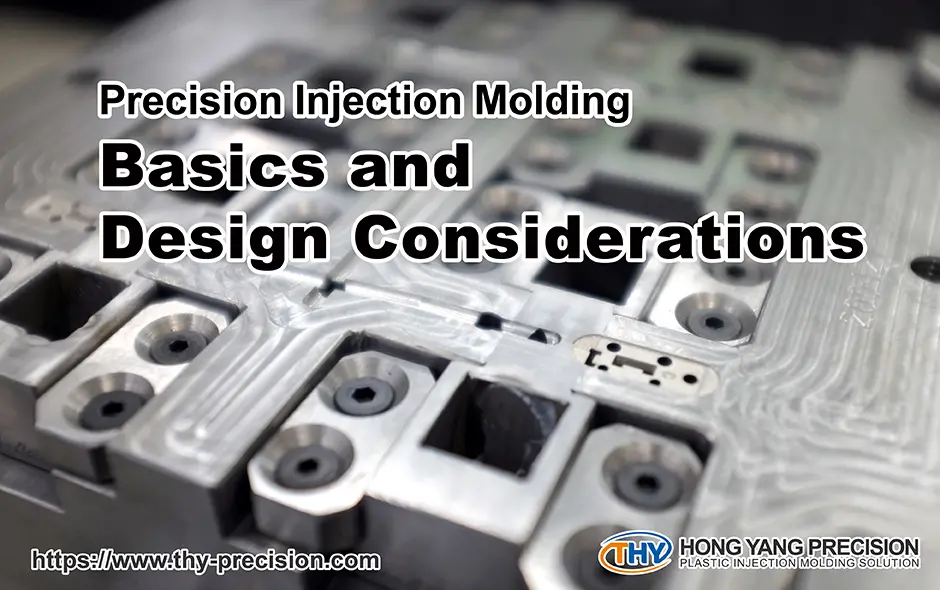
Creating outstanding products requires a deep understanding of precision injection molding design guidelines, which are critical for determining part quality and ensuring consistent production repeatability.
To minimize unnecessary costs in precision injection molding, this article will talk about the basic fundamentals of precision injection molding that are of primary concern to our clients and briefly discuss key design considerations within the precision injection molding process.
Table of Contents
Concept of Precision Injection Molding
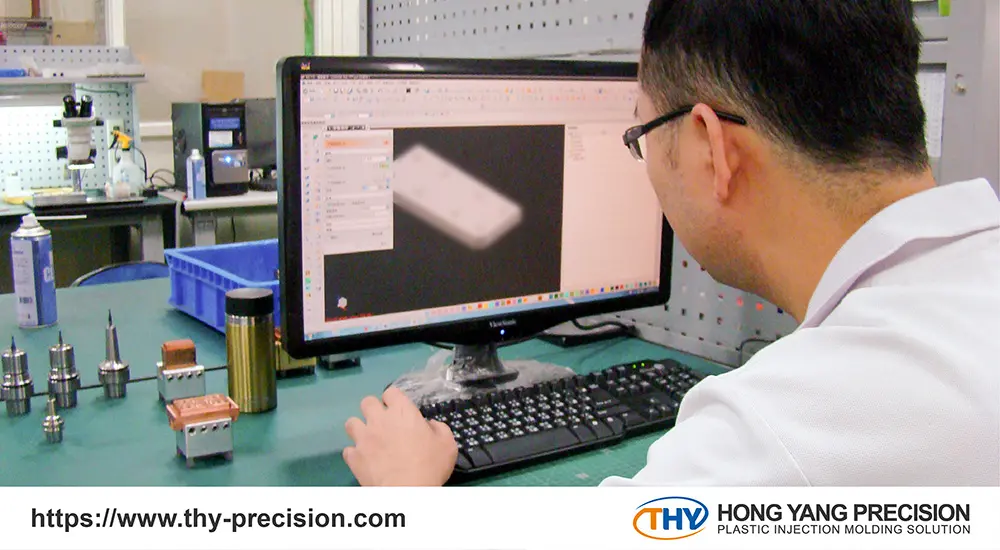
In recent years, the demand for precision in injection molding has significantly grown, especially for creating parts that are micro, feature complex designs, and possess diverse geometric shapes. This level of precision is critical for producing small-sized components across various industries.
Unlike traditional injection molding methods, which typically has a tolerance of 0.5 mm, precision injection molding excels in delivering exceptional dimensional control and the consistent production of parts with extremely tight tolerances, as fine as 0.01 mm, across large volumes.
Another factor influencing dimensional accuracy is the choice of machinery used in the process. Injection molding machines manufactured in Japan are renowned for their capability to produce extremely detailed and complex components.
Click here to learn more about types of injection molding machines.
4 Factors Affecting Precision Injection Molding Accuracy
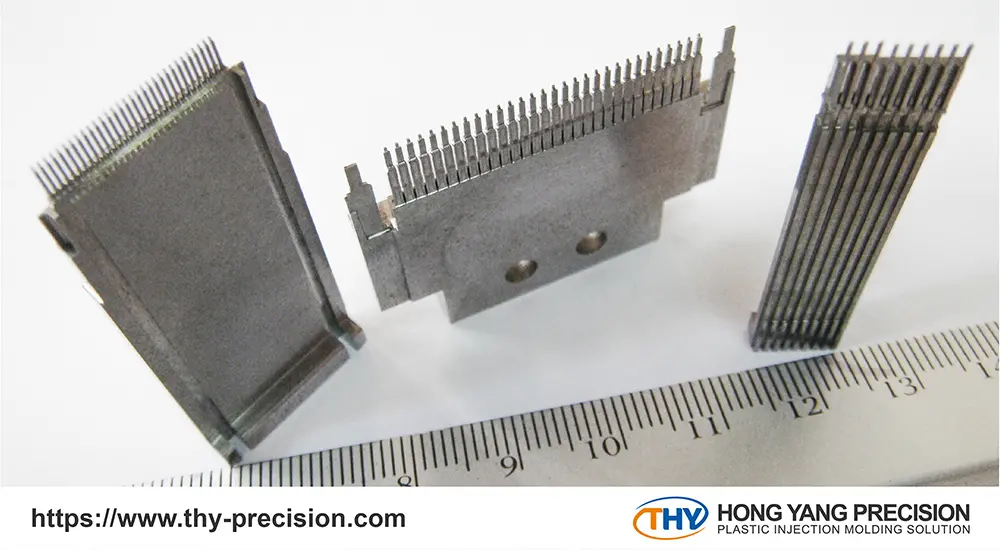
For clients who are less familiar with precision injection molding, we provide four primary considerations to bear in mind when preparing to manufacture small components.
Mold Design and Quality
Producing accurate components through precision injection molding depends on more than just advanced molding machines; mold design is equally critical in achieving high-precision outcomes. Engineers should pay attention to key design elements such as the mold cavity, mold base, parting line, gate location, and water circuit design.
Materialauswahl
Selecting the appropriate material for production marks just the beginning of the precision injection molding process, with the melt flow rate (MFR) emerging as a critical factor that shapes the journey thereafter. The MFR’s influence extends deeply into the molding operation, dictating the ease with which the material flows and fills the mold, thus directly impacting the overall quality and consistency of the final products.
Among the common materials selected in precision injection molding, Polycarbonate (PC), Acrylic (PMMA), and Polystyrene (PS) are three plastic materials adopted largely due to their favorable mechanical properties.
Molding Machine Parameter Control
While molding machines are pivotal in manufacturing high-precision products, the significance of parameters like clamping force, injection pressure, speed, and thermal management within these machines cannot be overstated. Beyond these technical specifications, precision injection molding also depends on rigorous environmental control.
Maintaining consistent temperature and humidity levels is essential for enabling the molding machines to produce uniformly sized products on a mass scale. This blend of precise machine settings and stable environmental conditions forms the cornerstone of successful precision injection molding operations.
Operator Skill and Experience:
While designers often prioritize mold design, superior materials, and top-tier equipment, the true linchpin in precision injection molding is the skill and expertise of the operator. Their knowledge and experience are crucial for maintaining high precision production and for navigating the challenges that accidentally arise during the manufacturing process.
An experienced operator should have a good understanding toward the characteristics of materials, be able to adjust the machinery, and interpret parameters to ensure the quality of production.
At THY, our strength lies in our team of highly skilled engineers and operators who ensure that our clients‘ products are manufactured efficiently and with the utmost accuracy. This expertise not only allows us to deliver excellent lead times but also results in cost savings for our clients, distinguishing our service in the industry.
3 Design Considerations for Precision Molding
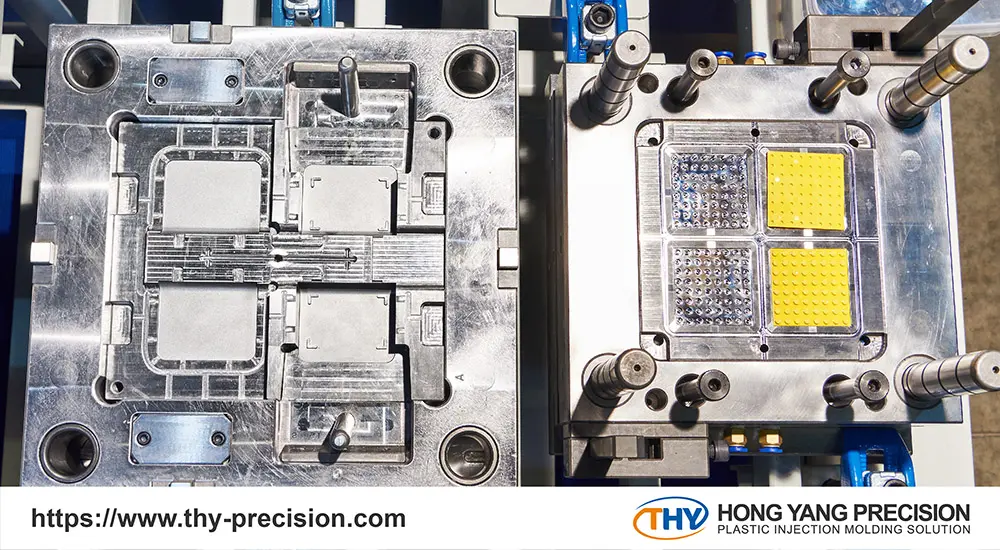
After knowing the factors that affect the accuracy of injection molded products, THY would also suggest on-site engineers three design considerations must be included: part design, mold design, and the surface finish of the parts.
Part Design
Incorporating draft into the design of a part for injection molding proves to be effective. By angling the sides of the part slightly instead of making them straight, it facilitates easier removal from the mold, helps prevent unwanted deformation, and enhances the efficiency of mass production in injection molding.
Formgestaltung
Designers need to consider not only the impact of part design but also how mold design influences the finished product’s accuracy and production efficiency. For instance, the design of undercuts must be carefully considered as they can sometimes hinder the removal of finished products.
Surface Finish
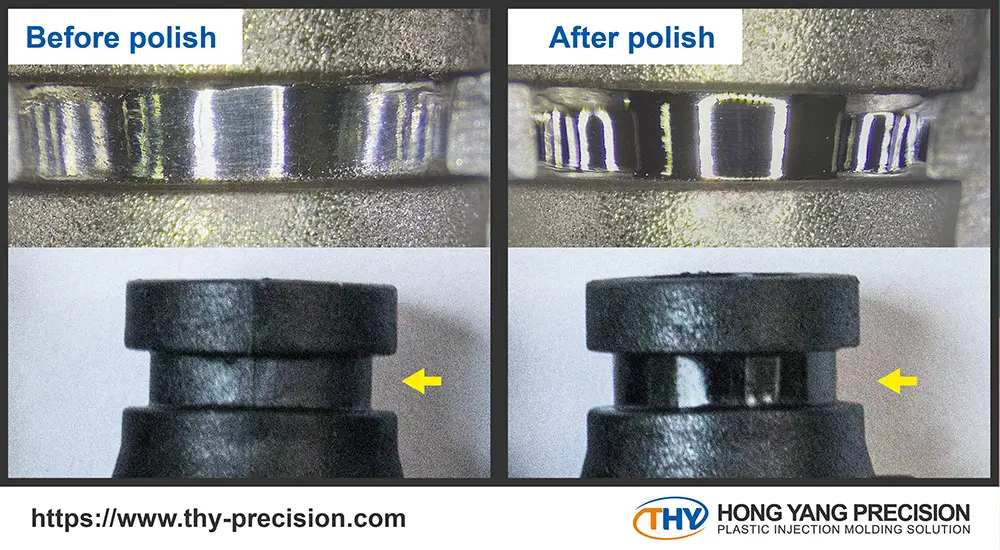
The surface finish of a component is crucial, particularly in precision injection molding, which is used to produce parts requiring high accuracy and strict tolerances. To prevent unexpected cracking and defects in the part’s surface finish, several important conditions must be considered.
We talk about six issues that commonly occur. For more detailed information on how to avoid these defects, please refer to design guidelines for injection molding.
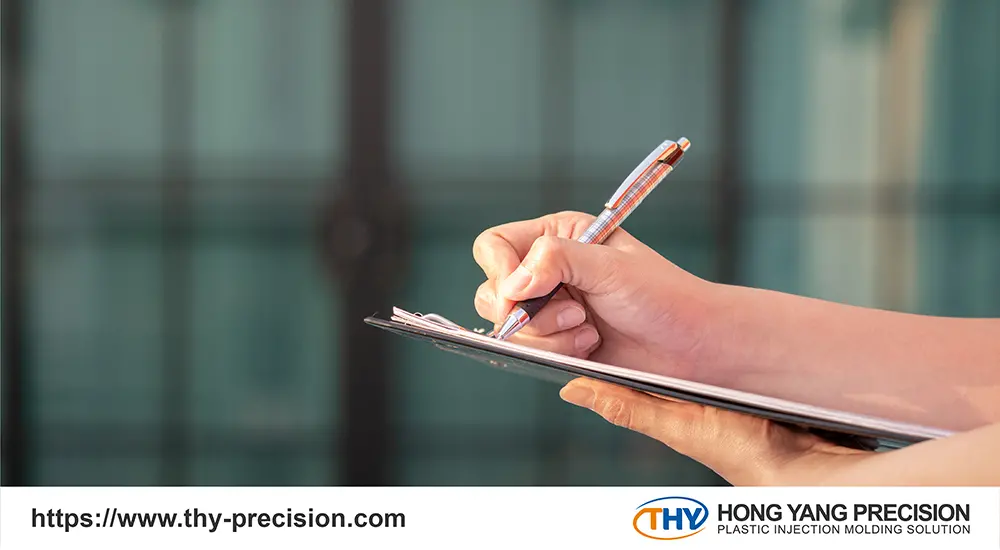
The absence of professional expertise in design and manufacturing can lead to increased production costs and extended development timelines, often resulting in unforeseen expenses. To overcome these obstacles and enhance your product’s profitability, our skilled R&D engineers have developed a comprehensive design knowledge for injection molding. We aim to deliver products that are both precise and reliable.
THY is a leading manufacturer of medical-grade and optical parts that require tight tolerances (±0.001 mm), supported by our state-of-the-art cleanrooms (Class 8 and Class 7) to cater to clients needing to avoid contamination. Our product line also complies with iso standards for medical devices, ISO 9001 and ISO 13485 standards.
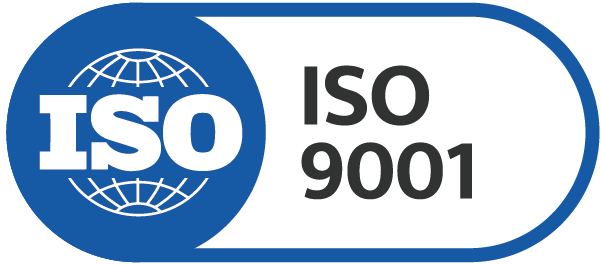
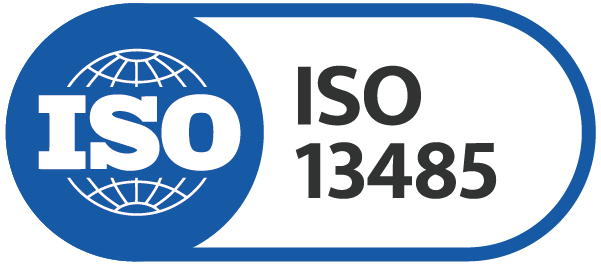
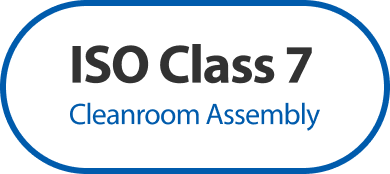
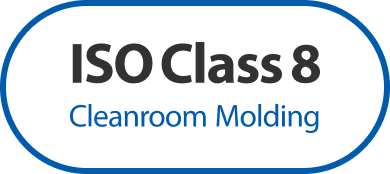
At THY, we are dedicated to transforming your part designs into reality. If you have any questions or encounter any design challenges, please feel free to contact us.