Published on 2024-01-22
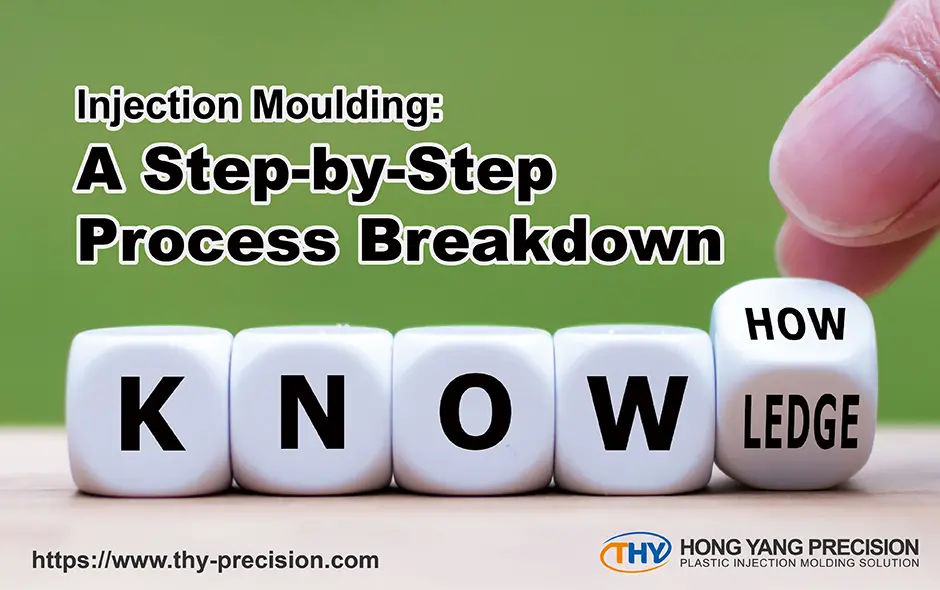
Plastic injection technology is a fundamental aspect of modern manufacturing, efficiently transforming raw plastic materials into a wide variety of unique products with diverse geometric shapes.
The injection moulding process step by step involves initially melting plastic pellets, then injecting them into precision-engineered moulds, and concludes with a cooling phase to solidify the final products. In the following article, we’ll take a deeper look into the process breakdown!
Table of Contents
What is Plastic Injection Moulding?
Plastic injection moulding is a widely used technique in the plastic industry. It revolves around the concept of heating and melting granular plastic pellets into a fluid state within an injection moulding machine.
This method is particularly efficient for mass-producing intricate items, as it allows for the creation of parts with various levels of complexity, precision, and design, using tailor-made steel moulds.
While the initial costs for mould development can impact the total expenses, plastic injection moulding remains low cost-per-part after mass production, owing to its effectiveness.
Plastic injection moulding distinguishes itself from other plastic manufacturing techniques like casting, dip moulding, slush moulding, blow moulding, and extrusion, primarily due to its exceptional ability to achieve superior surface finish quality, minimal waste, and maintain tight tolerances.
Plastic Injection Moulding Step by Step Process
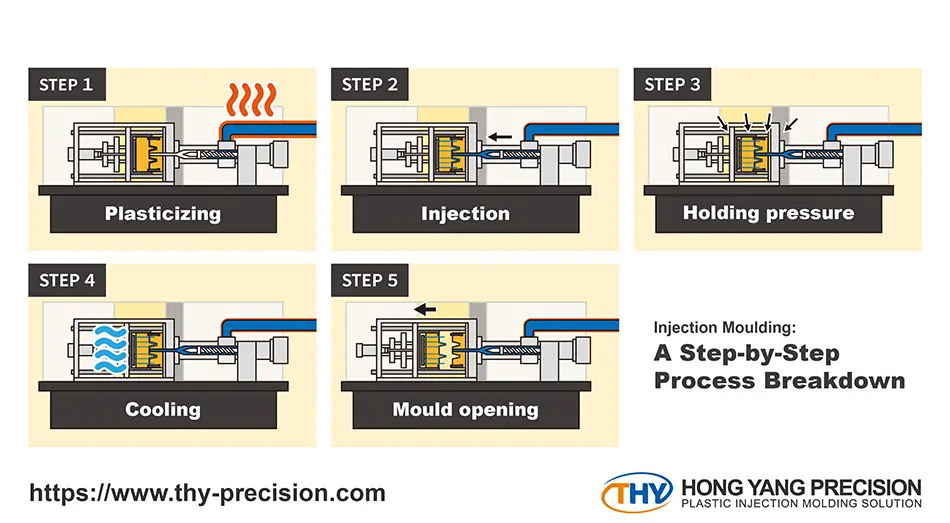
Plastic Injection moulding, renowned for its exceptional precision and clearance control, is extensively utilized in the production of medical, optics, electronics, and other industries requiring sophisticated product quality.
To provide a detailed insight into the injection moulding process, we will use the IOL(Intraocular lens) cartridge as a case study, illustrating each injection moulding process step by step.
Step 1: Plasticizing
In this phase, medical grade plastic pellets, namely Polypropylene (PP), are employed in the production of cartridges, which are subjected to melting temperatures specifically tailored to each cartridge type.
To facilitate this process, the moulding machine is calibrated to the optimal temperature, ensuring the efficient and complete dissolution of the PP plastic pellets.
Step 2: Injection
In this stage of the production, achieving the precise geometric shape is essential. This is accomplished by injecting the melted materials into a mould tailored specifically for the cartridge’s design.
At this time, it is necessary to adjust the parameters of the injection moulding machine according to the conditions of plastic injection moulding, to avoid subsequent issues, such as non-conforming dimensions and burrs etc.
Step 3: Holding pressure
At this stage, the molten plastic thoroughly fills the entire mould. Pressure is consistently applied to the mould to ensure that the liquid reaches every cavity so that the finished product exactly matches the mould’s design.
This step is crucial to prevent any deviations from the planned design, especially for the medical-used product.
Step 4: Cooling
After the molten plastic is poured into the mould, let it cool and solidify undisturbed for a designated period of time.
Once fully cooled and solidified, the product can be safely removed from the mould, ensuring it maintains its intended structure and quality. This step is key to preserving the integrity and specifications of the final product.
Step 5: Mould opening
Once the mould is opened, the solidified cartridge is meticulously extracted from the mould cavity. The fabricator then uses precision cutters to remove any excess material, fine-tuning the product to ensure it meets the specifications.
How to Control Quality of Plastic Injection Moulding?
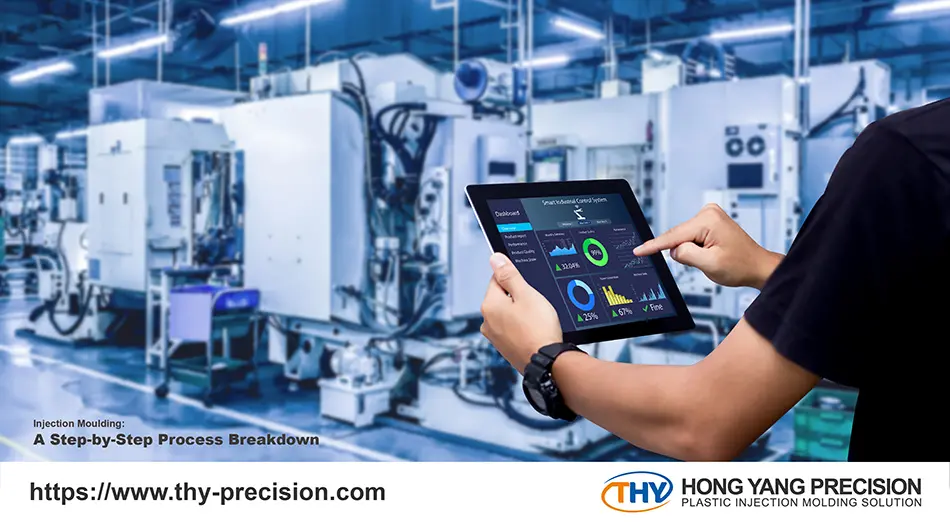
THY Precision is committed to exceptional production quality, leveraging state-of-the-art technologies such as part aligners and Automated Optical Inspection (AOI) systems. These tools enable automated and precise inspection processes, aligning with the rigorous standards of the ISO 13485 certification.
With ISO Class 8 clean room, manufacturers can mitigate contamination risks during the manufacturing process, a factor of paramount importance in medical product fabrication. To further enhance product quality, THY Precision has implemented an ISO Class 7 clean room specifically for assembly operations.
The combination of ISO 13485 standards and advanced clean room facilities empowers THY Precision to produce medical-grade products of the highest quality. The product range includes chamber filters, dialyzer filters, intravenous infusion drips, and bacteria filters, all manufactured to meet the exacting demands of the medical field.
Achieving Quality Finishes with THY Precision
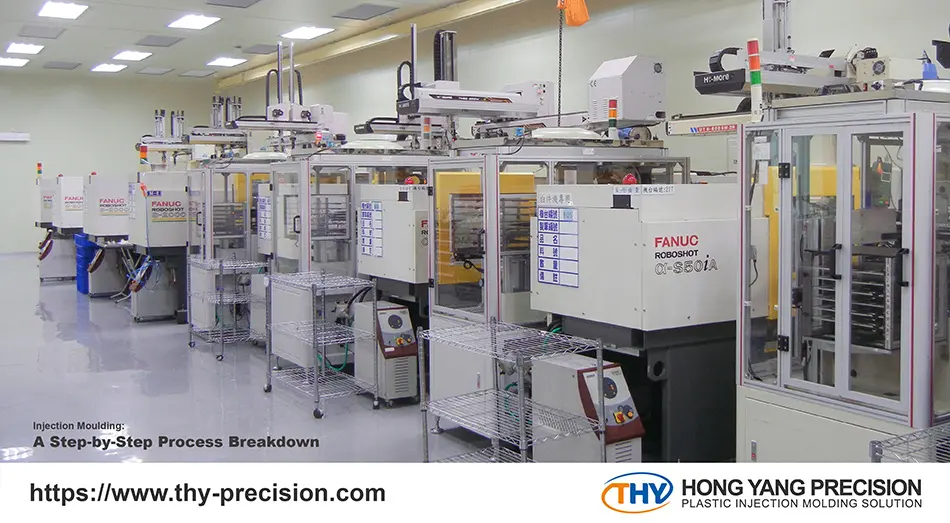
THY Precision, with its extensive expertise in OEM/ODM medical injection moulding, provides a comprehensive One-Stop Service to meet clients‘ requirements. Our service includes mould design, design for manufacture (DFM), design for assembly, Class 8 Cleanroom moulding and Class 7 cleanroom assembly.
THY specializes in the semi-automated and automated production of medical devices. Our engineering team and design-for-manufacturing system maintain product specifications and consistency throughout the process. We have the ability to meet the most challenging injection tolerance to ±0.001mm.
For clients considering crafting micro plastic parts with rigorous standards, THY can offer expert guidance. Our team of industry-leading specialists assists in evaluating the potential advantages and challenges before the production to meet the goal of efficient manufacturing.
For a comprehensive quotation, contact us today to discuss your project and the total quantity you demand!
Learn more: In-Depth Look at Injection Molding Machine Types & Uses