Published on 2025-02-20
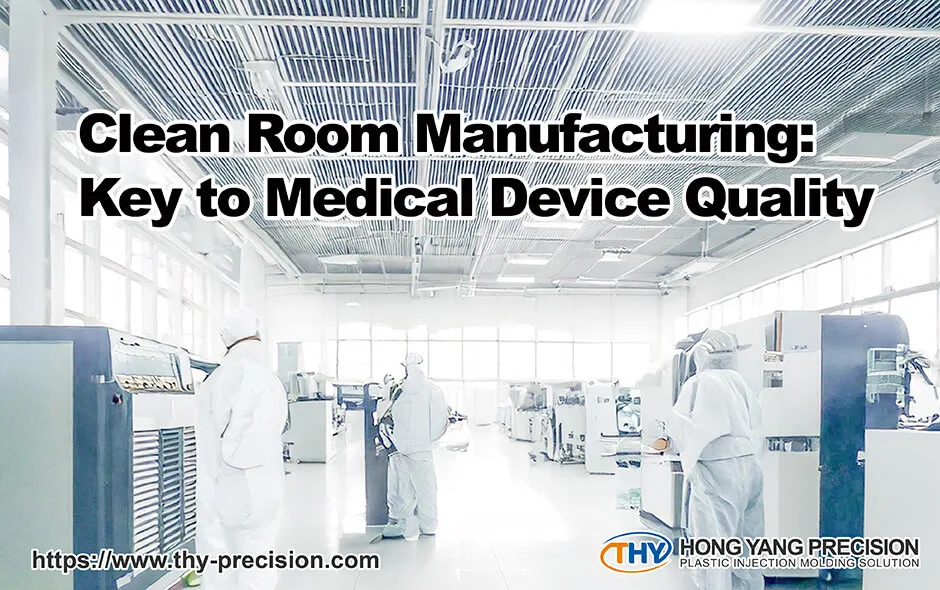
Clean room manufacturing is critical in meticulously controlled environments that minimize airborne particles and pollutants. These specialized facilities, known as clean rooms, are essential in industries where microscopic impurities can compromise product quality.
Table of Contents
What is a Clean Room?
Clean rooms implement strict controls through advanced environmental management systems. These sophisticated systems meticulously regulate temperature, humidity, and airflow while utilizing high-efficiency particulate air (HEPA) and ultra-low particulate air (ULPA) filters to ensure optimal conditions.
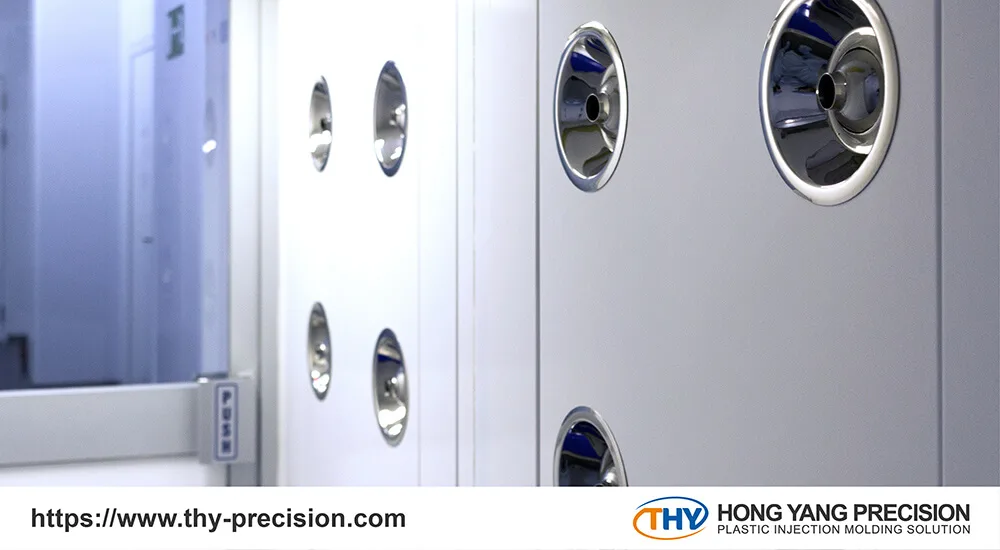
Furthermore, positive pressure systems prevent external contamination, while specialized materials like epoxy resins are strategically applied to walls, floors, and ceilings to facilitate thorough cleaning and efficient maintenance.
The International Organization for Standardization (ISO) classifies clean rooms based on the concentration of airborne particles. Two standard classifications are ISO 7 and ISO 8 cleanrooms. The following outlines the specifications of these two standards:
• ISO 7 Standards for Clean Rooms
Particle count (≥0.5 µm): No more than 352,000 particles per cubic meter
Particle count (≥1 µm): No more than 83,200 particles per cubic meter
Particle count (≥5 µm): No more than 2,930 particles per cubic meter
• ISO 8 Standards for Clean Rooms
Particle count (≥0.5 µm): No more than 3,520,000 particles per cubic meter
Particle count (≥1 µm): No more than 832,000 particles per cubic meter
Particle count (≥5 µm): No more than 29,300 particles per cubic meter
Clean rooms are vital across various industries, particularly in medical manufacturing. They enable the production of sterile components such as surgical instrument casings, IV set components, and implantable devices.
Other industries benefiting from clean room technology include electronics manufacturing, aerospace component production, and pharmaceutical processing, where maintaining a controlled environment is essential for ensuring product quality and safety.
Why is Clean Room Manufacturing Important?
Clean room manufacturing environments are essential for producing critical medical instruments and components. The controlled environment of a clean room ensures these medical devices meet the stringent requirements for patient safety and operational reliability through exact fabrication in sterile conditions.
Leukocyte reduction filters are a prime example of this precision-driven process. They are designed to remove white blood cells from blood transfusion products, and the manufacturing process demands meticulous attention to cleanliness standards to prevent potential immune reactions in patients.
Similarly, many other medical devices rely on stringent contamination-free production conditions to ensure reliability and effectiveness. For instance, sophisticated filtration devices, surgical instrument casings, IV set components, and endoscopes must all maintain high standards of cleanliness to preserve their functionality and precision.
Furthermore, clean room manufacturing plays a vital role in plastic injection molding processes for medical devices. These sterile conditions not only reduce production defects but also significantly enhance the reliability of the final products. This is particularly critical for sensitive medical equipment such as implantable devices and diagnostic tools, which must comply with strict FDA standards and ISO 13485 regulations for medical device manufacturing.
Key Features of Clean Room Manufacturing
Clean room manufacturing stands out due to its advanced control systems and innovative technologies that ensure consistency and precision. Here are the key features:
1.Medical-Grade Facility Design
Clean rooms are strategically divided into specialized zones to facilitate the simultaneous production of various medical devices while preventing cross-contamination.
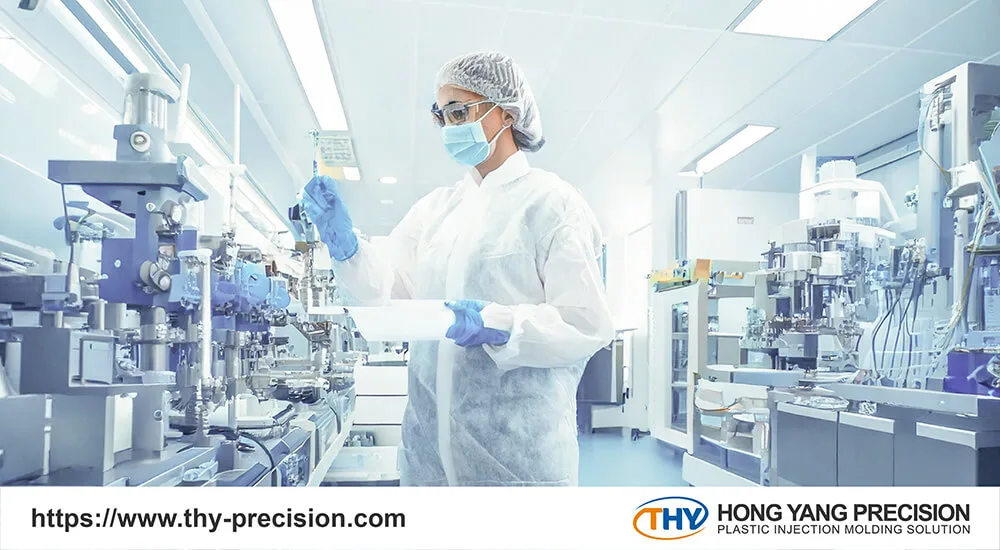
2.Precision Air Management
Advanced HVAC and laminar flow systems maintain the conditions required for sterile medical manufacturing. This is particularly crucial for respiratory devices and surgical instruments, where air purity directly impacts product safety.
3.Strategic Pressure Control
Multi-zone pressure gradients protect different medical devices during production, with the highest pressures maintained in areas producing critical implants and diagnostic components.
4.Rigorous Quality Monitoring
Continuous environmental monitoring ensures compliance with medical device manufacturing standards, focusing on parameters critical for patient safety and product efficacy.
5.Adaptable Manufacturing Space
Modern facilities are designed to accommodate rapid medical technology evolution, allowing quick adaptation to new device production requirements and regulatory changes.
6.Precision Automation Systems
Robotic systems handle delicate medical device assembly tasks, ensuring consistent quality while minimizing contamination risks in sterile product manufacturing.
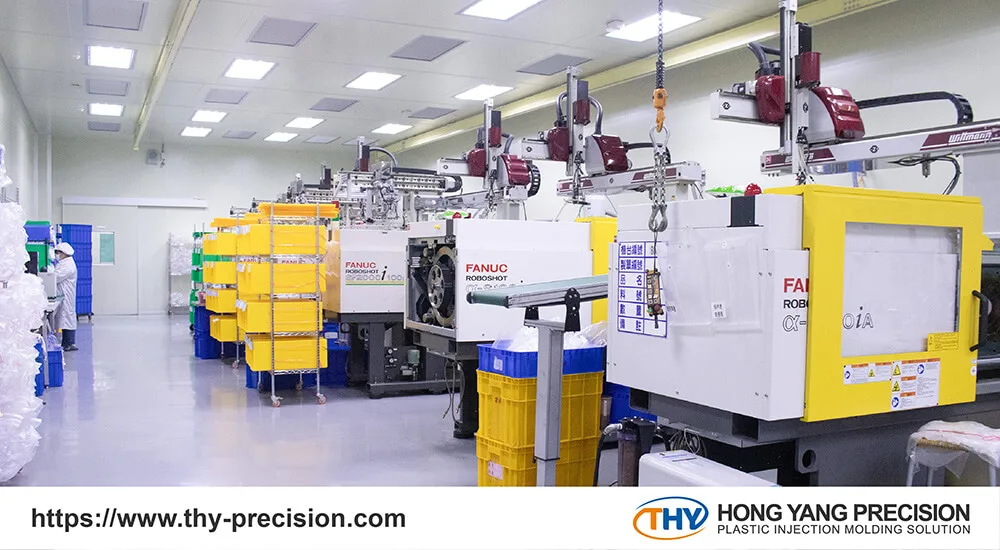
7.Smart Monitoring Integration
AI and IoT systems provide real-time monitoring of critical parameters during medical device production, ensuring immediate detection of deviations from required standards.
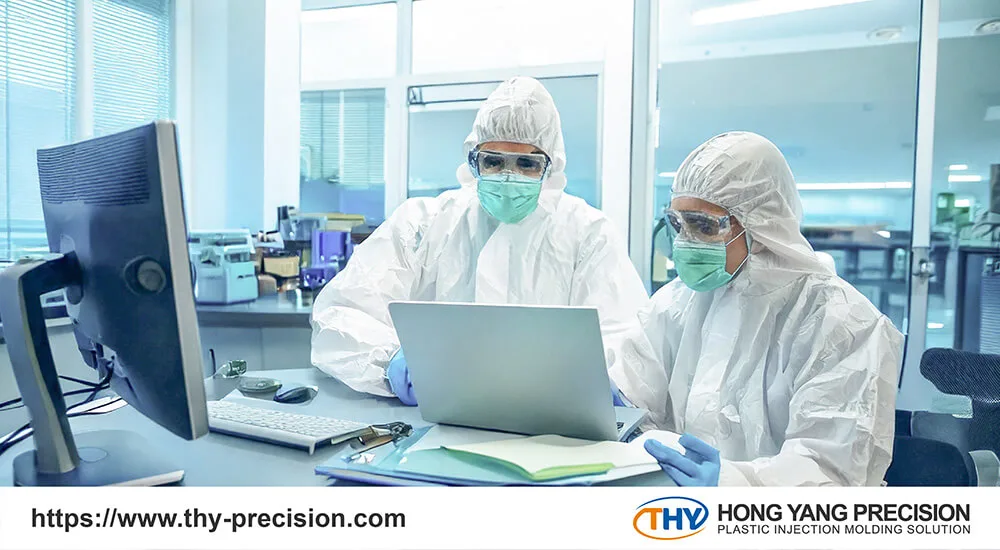
3 Advantages of Clean Room Manufacturing in Medical Applications
Clean room manufacturing offers several benefits that make it indispensable for medical applications:
1.Contamination-free production
The pristine environment ensures the highest level of protection for critical medical components, from sophisticated diagnostic equipment to life-supporting devices. This controlled setting is essential for manufacturing biological sensors and tissue-contact devices, where microscopic contaminants could compromise therapeutic effectiveness or patient outcomes
2.Stringent quality control and regulatory compliance
Clean room manufacturing provides comprehensive quality verification that extends beyond standard protocols. The environment enables manufacturers to maintain detailed environmental monitoring records, facilitating seamless compliance with FDA guidelines and ISO 13485 certifications while establishing robust validation processes for each production batch.
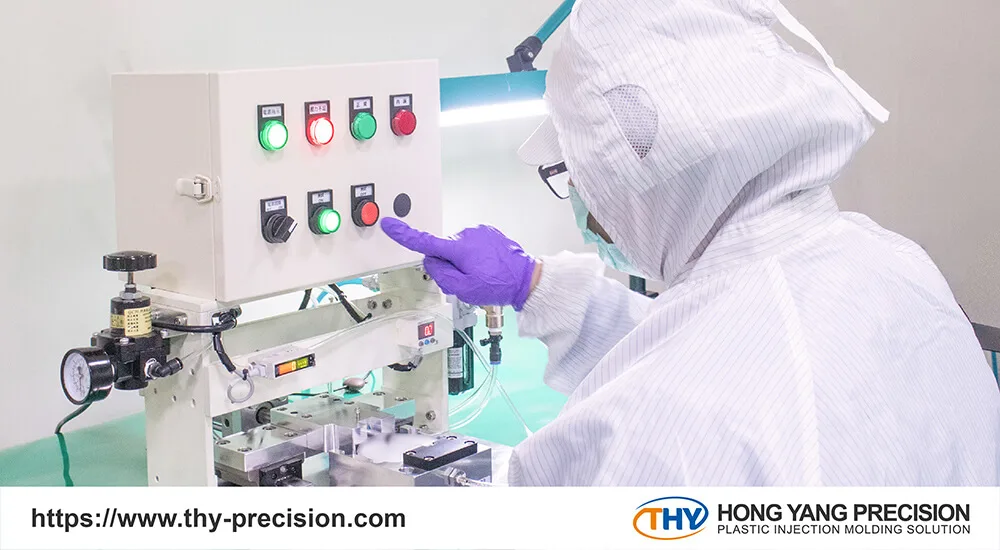
3.Enhanced Patient Safety and Product Reliability
The meticulously controlled manufacturing conditions directly contribute to clinical success rates. This level of control is particularly crucial for producing precision medical instruments and life-critical devices, where consistent performance can significantly impact therapeutic outcomes. Careful oversight throughout the production process ensures that each device meets its intended medical purpose with maximum reliability.
Clean Room Manufacturing at THY Precision: Excellence Delivered
THY Precision has established itself as a leader in clean room manufacturing, with extensive experience in custom plastic injection molding for critical medical applications. Our expertise in medical device manufacturing spans intricate surgical instruments and complex diagnostic equipment components, providing best-in-class high-precision tooling and OEM plastic component manufacturing services across the medical devices, optics, and electronics sectors.
Our clean room manufacturing operations are backed by ISO 13485 and ISO 9001 certifications, demonstrating our commitment to maintaining the highest international standards in medical device production.
Ready to take the next step? Contact us today to learn more about our tailored solutions or request a customized quote. For further information, visit our website or connect with us!
Learn more:
A Guide to Clean Room Plastic Injection Molding [2024]