Published on 2024-08-01
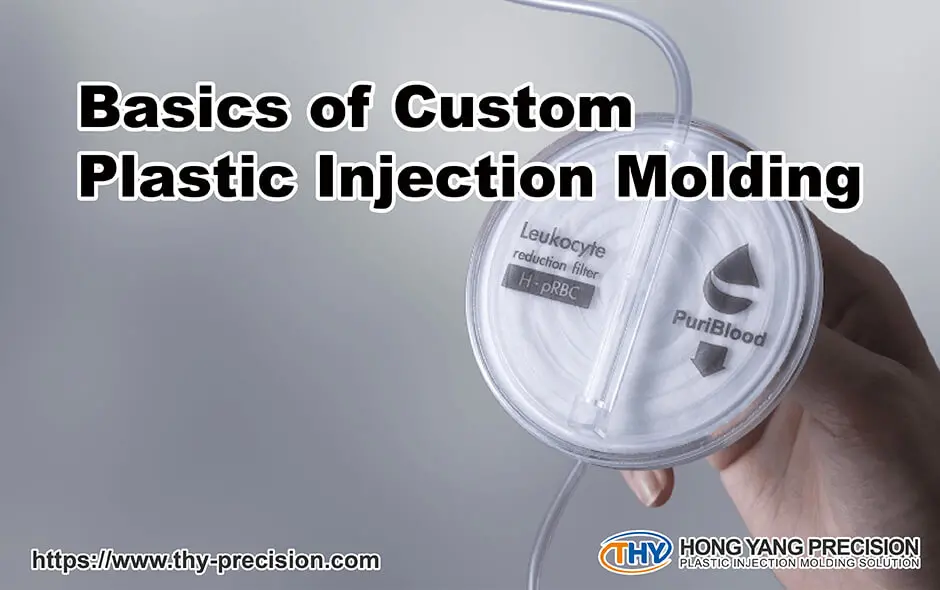
Plastic injection molding is a cornerstone of modern manufacturing known for its precision and efficiency. By converting raw plastic materials into complex, high-quality parts, this process has become indispensable across numerous industries.
This article delves into the essential principles and step-by-step procedures of the injection molding process and covers everything you need to know. Continue reading to discover how plastic injection molding can enhance manufacturing capabilities and product quality.
Table of Contents
What is Plastic Injection Molding?
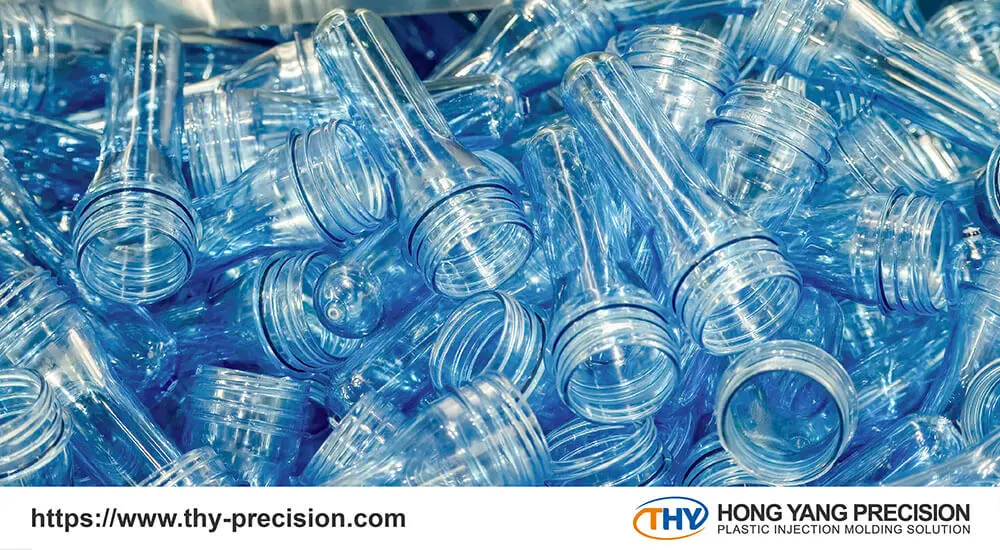
Plastic injection molding is a manufacturing process that produces parts by injecting molten plastic into a mold. The basic principles involve melting plastic pellets, injecting the molten plastic into a mold cavity, cooling it until it solidifies, and then ejecting the final product.
For industries aiming for high-precision parts, the tolerance standard is strictly defined to maintain product quality and consistency. The All-electric injection machine is perfect for demanding sectors as it reduces the risk of mold crush. Unlike hydraulic machines, all-electric injection molding machines offer greater control and consistency. They provide precise movements, consistent pressure, and improved repeatability, essential for achieving high precision and tight tolerance in the final products.
Those interested in exploring the machines used in manufacturing can learn more about injection molding machine types.
How does Plastic Injection Molding Work?
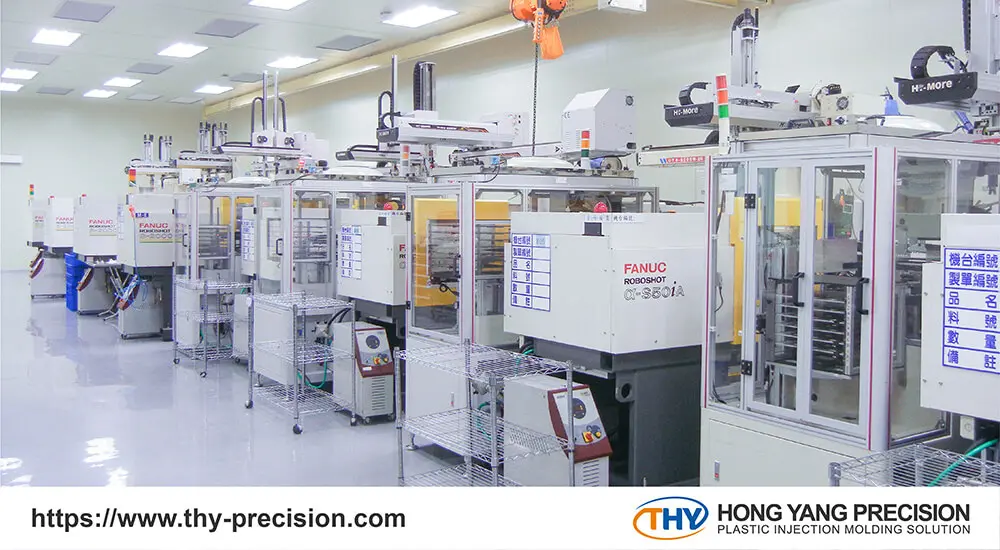
Plastic injection molding involves several critical steps, each contributing to producing high-precision plastic parts. Here is an explanation of the general plastic injection molding process:
● Mold Design and Fabrication
The mold is a precision tool that determines the shape and features of the final plastic part. It is typically made from durable materials like steel or aluminum to withstand the high pressures of the injection process. The design must consider the part’s geometry, tolerances, and specific requirements, such as cooling channels and ejector pins.
● Material Selection and Preparation
Typically, thermoplastics are preferred for injection molding because they are more adaptable for creating intricate shapes. When the resin is determined, the plastic pellets are set to dry before production starts.
● Injection and Cooling
The plastic pellets are heated and injected into the mold under high pressure. Proper cooling channels within the mold manage and speed up the cooling process, affecting the part’s accuracy and finish.
● Ejection and Finishing
Once the plastic solidifies, the mold opens, and the part is ejected. Additional finishing processes, like hot stamping, screen printing, and spray painting, may be applied to meet final specifications.
You can explore the injection moulding process step by step for a more detailed guide.
Types of Plastic Injection Molding Techniques
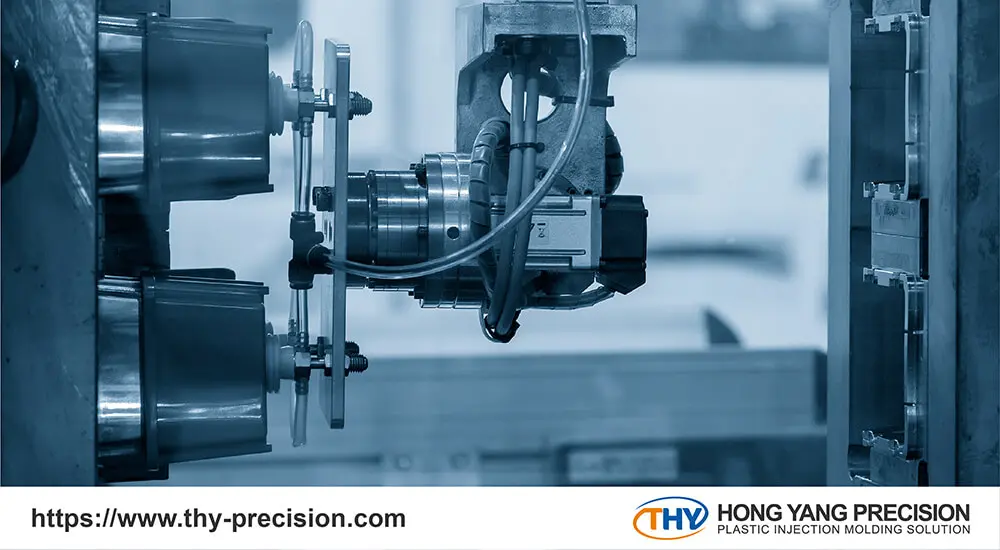
Plastic products formed through injection molding can offer essential appearance quality, but their aesthetics and texture can be further enhanced to another level through secondary processing. Plastic injection molding encompasses several specialized techniques, each suited for different applications and requirements. The most common techniques include:
● Family Tooling
It allows multiple parts to be molded simultaneously using a single mold. It is cost-effective and efficient for producing different parts that are part of the same assembly.
● Insert Molding
This technique involves placing a preformed metal component into the mold and is widely used for creating products that require solid and durable inserts within plastic parts.
● Over-Molding (Two-Shot Molding)
Just like the name assumes. One material is molded over a second material to create a composite part, such as a soft grip on a complex tool handle.
● Multi-Shot Injection Molding
This advanced method involves sequentially injecting different materials into a single mold to create multi-material parts in a single molding cycle.
For further details on plastic injection molding techniques, refer to the design guidelines for injection molding.
Plastic Injection Molding Materials
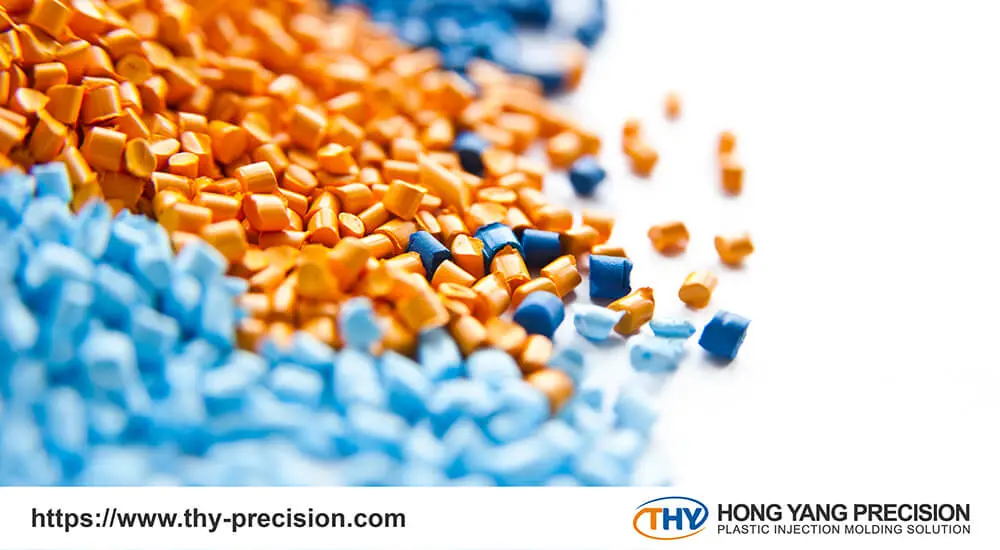
Selecting the right material is essential for the injection molding process, as it affects project performance, cost, and production time. This important decision can be challenging.
To help with this, THY Precision has created a quick guide to injection molding materials and their properties to assist you in finding the best option.
- Application Requirements: The material must meet the specific purpose of industry needs, such as strength, flexibility, and chemical resistance.
- Operational Lifespan: Durability or impact resistance is considered to be sufficient to withstand the product’s expected lifespan.
- Stresses Involved: If the final product encounters mechanical, thermal, or environmental stresses, the toughness of the resin should be higher.
- Aesthetic Considerations: The appearance of the final product, including color and finish, may influence material choice.
- Budget Constraints: Cost is always a factor, and finding a balance between performance and price is of high priority.
Common Injection Molding Plastics
Here is a table summarizing some of the most commonly used resins in plastic injection molding:
Material | Advantages | Applications |
Polyethylene(PE) | High impact resistance, low-cost | Containers, bottles, plastic bags |
Polystyrene(PS) | Easy to mold, good dimensional stability | Packaging, disposable cutlery |
Polyamide/Nylon (PA) | High strength, excellent wear resistance | Gears, bearings, automotive parts |
Polypropylene(PP) | Chemical resistance, fatigue resistance | Packaging, automotive components |
Acrylonitrile Butadiene Styrene (ABS) | Tough, high-impact strength | Consumer electronics, toys |
For more details on choosing the right resin for injection molding, please refer to our comprehensive guide.
Quality Inspections and Finishing Options
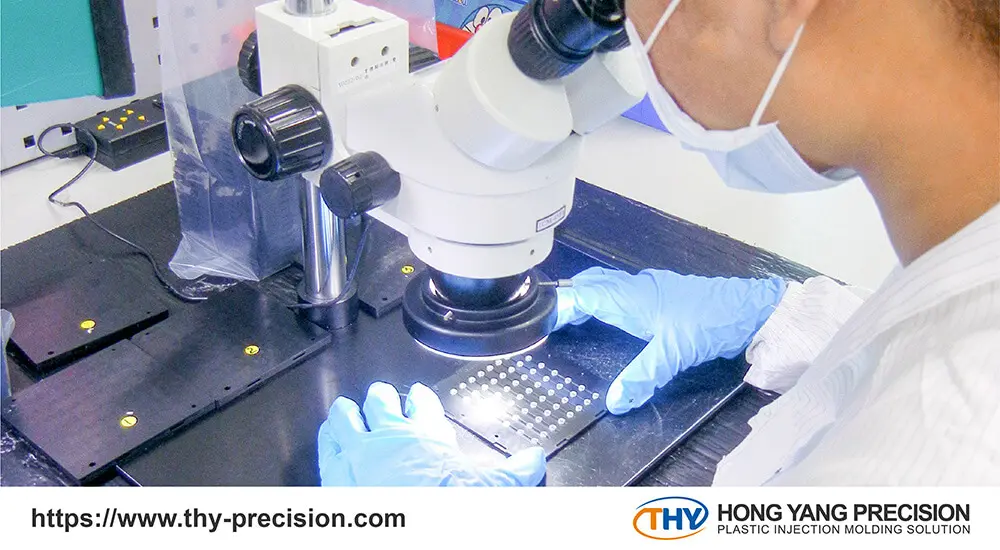
Quality inspections are implemented at every production stage to meet the highest standards. THY Precision employs a range of advanced inspection tools to maintain precision and quality so that clients can choose from various services depending on their project requirements, including:
- Ultra-High Accuracy Coordinate Measuring Machine (CMM)
- Non-Contact Video Measuring System
- Roundness Measuring Instrument
- Metrology Instrument
- Composite Image Measurement
These measures ensure that each part meets stringent quality criteria, essential for applications requiring high precision and compliance with ISO standards for medical devices.
Post-Processing Options at THY Precision
Depending on the project’s needs, we also offer several post-processing services to enhance and customize the final product:
- Ultrasonic Welding
- Spray Paint and Coating
- Insert Installation
- Component Assembly
- Pad Printing
- Laser Engraving
- Functional Testing
- Packaging Design and Development
These options allow clients to achieve the desired functionality and aesthetics while maintaining the high standards required in their industry.
THY Precision has extensive experience producing healthcare-related parts, understanding that precision and quality are paramount in the medical industry. Operating in an ISO 8 clean room environment, our engineers ensure that products are free from contaminants and meet the rigorous meaning of ISO 13485 standards. This capability is critical for producing medical devices and other products where cleanliness and sterility are paramount.
For more information on the benefits and processes of clean room injection molding, visit our detailed guide.
Applications of Plastic Injection Molding
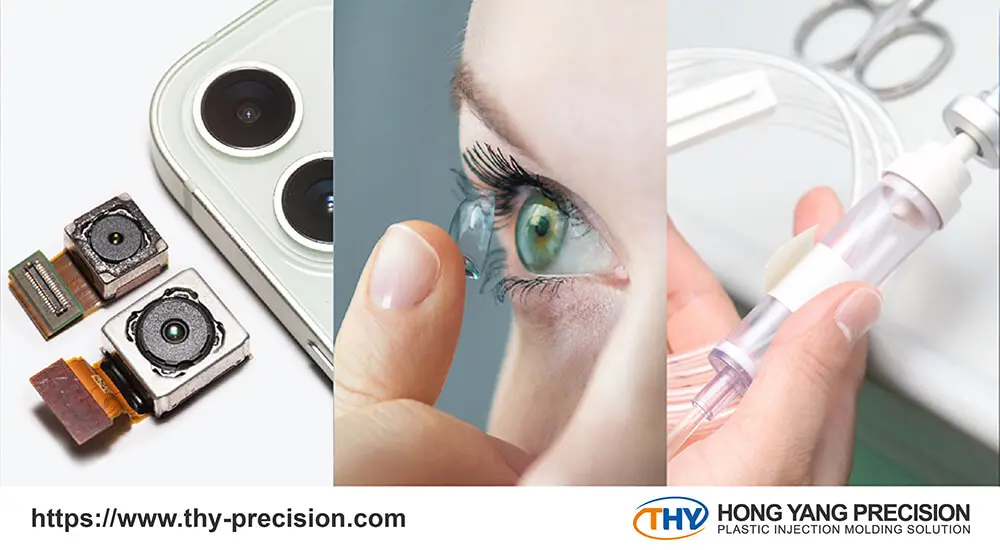
Due to its efficiency and precision, plastic injection molding is widely used across various industries. Here are some of the key industry applications:
● Medical
The medical industry relies heavily on plastic injection molding to produce high-precision components such as syringes, implants, and diagnostic devices. This method is particularly suitable for medical device plastic injection moulding thanks to its ability to produce parts with tight tolerances and consistent quality.
● Optical
Precision plastic injection molding is crucial for producing components like lenses and light guides in the optical industry. It ensures the optical clarity and exact specifications required for high-performance optical applications.
For more information, check out our detailed guide on injection molding optical lenses.
● Electronics
In the electronics sector, plastic injection molding is used to manufacture housings, connectors, and other critical components.
Micro injection molding is an advanced variation of this process, which is pivotal in today’s industry. Celebrated for its high precision, with tolerances ranging from 10 to 100 microns, it enables the production of components weighing less than 1 gram. This level of precision is essential for the performance and safety of electronic devices.
● Automotive
Widely used in the automotive industry, plastic injection molding can create more complex shapes and integrate various features into one single part. Typical products include dashboards, bumpers, and interior trim parts.
● Aerospace
The aerospace industry uses plastic injection molding to produce lightweight yet strong components. The ability to meet stringent quality standards and produce parts with complex geometries makes it suitable for aerospace applications.
Whether you need high-precision components for medical devices, optical parts, or intricate electronic components, THY Precision offers state-of-the-art technology and expertise to meet your requirements. Discover how our advanced processes, clean room, and micro injection molding can improve product quality and performance.
Ready to get started? Contact us today to learn more about our services and request a quote tailored to your needs. Visit our website or reach out to our team for more information.
Hong Yang Precision Industry Co., Ltd.
Sales email: sales@thy-precision.com
No.107, Zhongzheng Rd., Puyan Village, Puyan Township, Changhua, 516, Taiwan
Tel: +886-4-8653625
Fax:+886-4-8654175