Published on 2024-08-16
![A Guide to Clean Room Plastic Injection Molding [2024]](https://www.thy-precision.com/wp-content/uploads/2024/08/A_Guide_to_Cleanroom_工作區域-1-jpg.webp)
In industries like healthcare, pharmaceuticals, and biotechnology, cleanliness is an absolute necessity. A single spec of dust can contaminate a life-saving drug or compromise a medical implant. That’s why clean room injection molding has become an indispensable part of manufacturing in these industries.
Table of Contents
What is Clean Room Injection Molding?
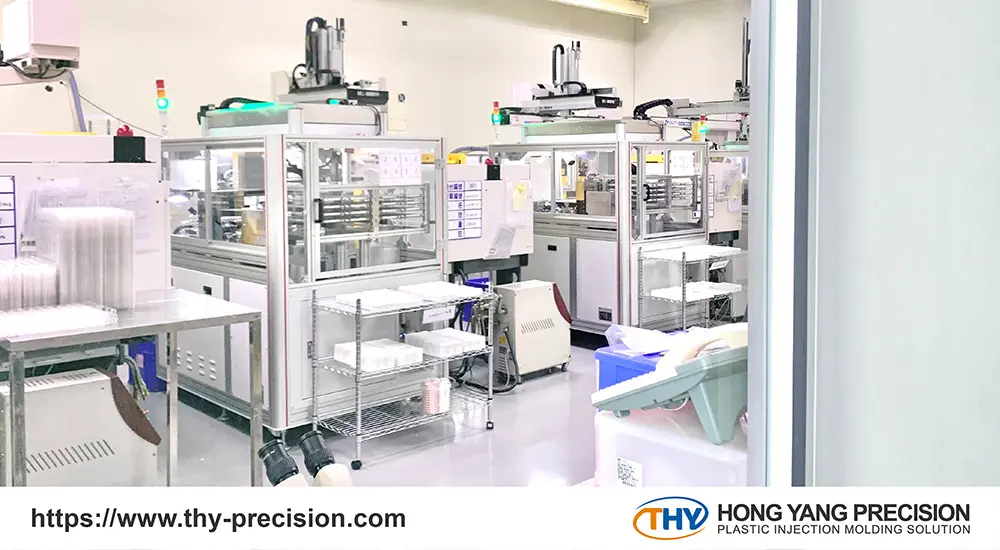
Clean rooms are highly controlled environments that minimize the risk of airborne particles getting into products or equipment. They prevent dust, dirt, and microbes from contaminating sensitive materials.
In injection molding, a clean room provides a sterile space to melt plastic resins, inject them into molds, and cool them off. They aim to ensure that the final products are safe and effective. Below is the common industries that require cleanroom environments:
● Medical Industry
With the help of clean room injection molding, medical manufacturers can safely provide quality-assured products to hospitals, clinics, and patients. This process ensures that medical devices are safe, ultimately improving patient care.
They can produce a wide range of sterile and safe components, such as:
- Surgical instruments
- Implants
- Drug delivery systems
- Diagnostic equipment
● Pharmaceutical Industry
The pharmaceutical industry takes cleanliness and hygiene to a microscopic level. Clean rooms help manufacturers create products that adhere to strict quality control standards and regulatory compliance.
For example, these products benefit from the pristine conditions of clean rooms:
- Drug containers
- Medical devices
- Diagnostic tools
- Packaging materials
● Biotechnology Industry
Biotechnology workers know how important it is to stay clean. They often work with sensitive biological materials like cells, tissues, and microorganisms. Clean rooms help maintain a sterile environment and avoid contamination.
Clean rooms help them successfully create devices that require high levels of sterility, like:
- Bioreactors
- Microfluidic devices
- Tissue engineering
- Gene therapy delivery
Classifications of Clean Room
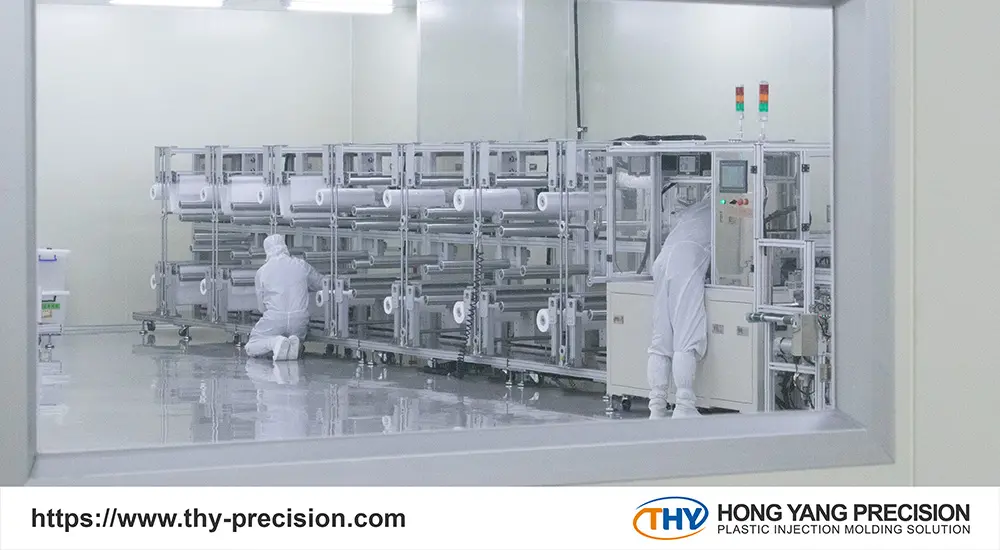
Clean rooms are classified based on their level of cleanliness, which is determined by the number and size of particles allowed per cubic meter of air.
Two primary standards used for clean room classification are:
ISO 14644-1 (Formerly known as FS 209E)
ISO 14664-1 is the current international standard clean room classification system. It classifies clean rooms into ranges from ISO 1 (the cleanest) to ISO 9, each with a specific limit for particles in the environment.
Among these standards, ISO 8 is commonly used in medical device manufacturing. Learn more about these classifications in this article: What is an ISO 8 Cleanroom? Principles & Requirements
Fs 209E is an older US federal standard that ISO standards have mostly replaced. Although some industries, like semiconductor manufacturing, still use this as a benchmark. Classifications range from Class 1 (the strictest) to Class 100,000 — each class also has a specific particle count.
ISO 13485
Medical device manufacturing adheres to ISO 13485, a global quality management system standard. While it doesn’t classify clean rooms, It’s in place to safeguard the quality and safety of medical devices produced in clean room environments.
Key aspects of ISO 13485 for clean room injection molding:
- Risk management: Identifying and mitigating risks related to contamination throughout the product life cycle
- Design controls: Ensuring medical devices are designed with cleanliness and sterility in mind, with the right materials.
- Production processes: Maintaining strict control over production processes, including cleanroom operations, disinfection procedures, personnel training, and monitoring systems.
- Quality assurance: Implementing a systematic approach to address any quality issues, such as contamination, and preventing them from happening again.
Clean Room Injection Molding Requirements
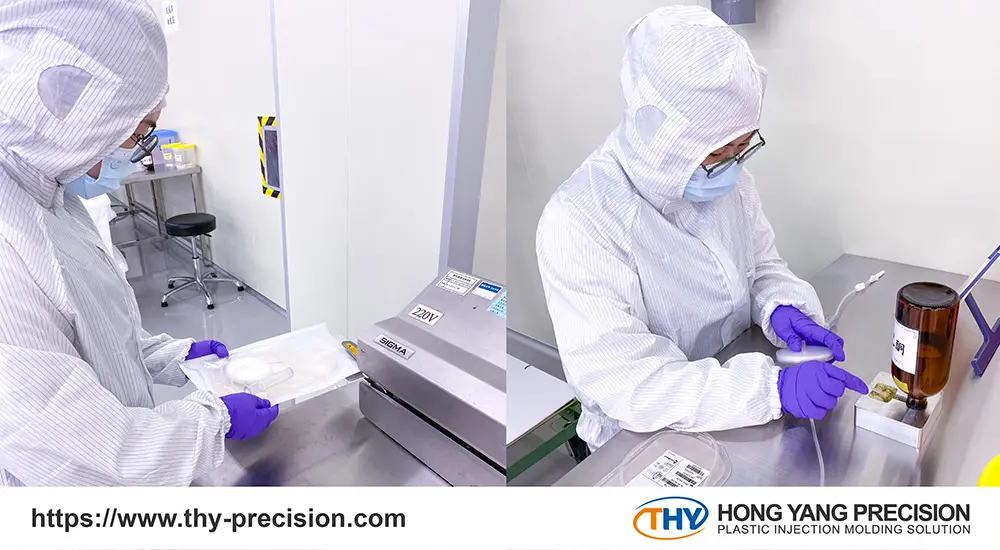
To maintain ISO standards, clean room injection molding facilities must follow strict requirements:
● Filtration System
High-Efficiency Particulate Air (HEPA) filters are essential in injection molding. They catch and remove 99.9% of microparticles from the environment.
It’s so effective that clean rooms are essentially classified based on the number of particles allowed per cubic meter of air.
Clean rooms sometimes use Ultra Low Penetration Air (ULPA) filters, which provide even higher filtration that can catch particles invisible to the naked eye.
● Airflow
Clean rooms have specialized airflow systems to control the movement of air and keep the environment clean. There are two types of airflow:
- Positive pressure airflow: The air pressure inside the clean room is higher than outside, causing air to flow outward when doors are opened. This prevents contaminated air from entering the clean room.
- Negative pressure airflow: The air pressure inside the cleanroom is lower than outside, causing air to flow inward when doors are opened. This is used to prevent hazardous materials from getting out of the clean room.
Airflow can also be classified as laminar or turbulent:
- Laminar airflow: Air flows in one direction in a smooth pattern, minimizing turbulence and the spread of particles.
- Turbulent airflow: Air flows in an unpredictable pattern, with eddies and swirls that distribute the particles.
Other requirements
Besides filtration and airflow, clean room injection molding facilities must also control:
- Temperature: A stable temperature prevents condensation and microorganisms from growing.
- Humidity: The right humidity level prevents static electricity, which can attract and spread particles.
- Pressure airflow: Clean rooms have higher air pressure in specific areas to control airflow and prevent contamination.
Clean Room Injection Molding Operating Procedure
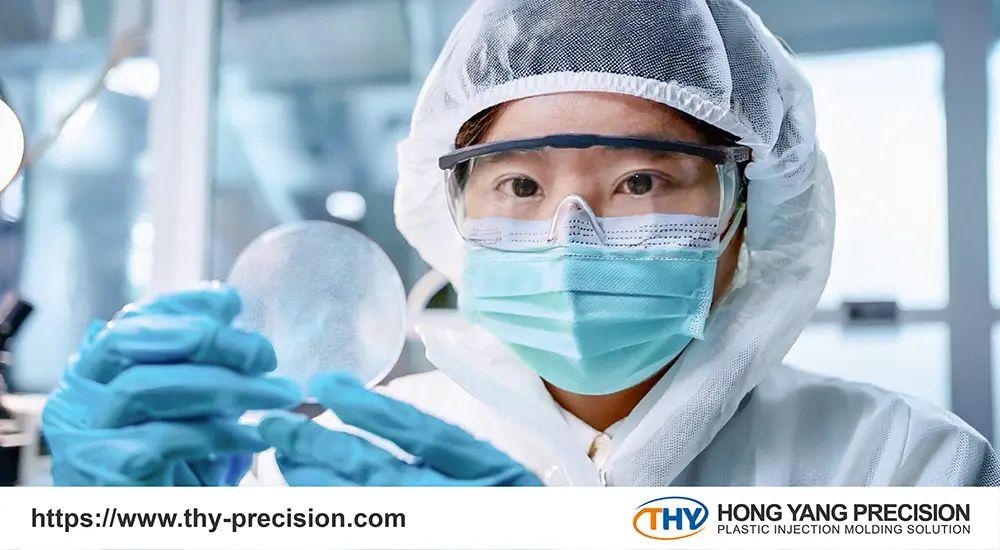
Inject molding in clean rooms has a strict operating procedure to ensure the product manufactured is safe and effective:
1. Material preparation
Raw plastic resins are selected and prepared according to strict quality control standards. This often includes drying or pre-heating the resin so that they are easier to process.
2. Manufacturing
The resins are melted and injected into precision molds inside the clean room. Temperature, pressure, and injection speed, are controlled to achieve the desired product quality and consistency. Click here to know more details about how injection molding works.
3. Assembly
If there are multiple molded components, they are assembled into the final product using adhesives or fasteners.
4. Packaging
Products are packaged in specialized containers or packaging materials to protect against contamination during storage and transportation.
5. Testing
Quality control tests, such as visual inspection, dimensional measurements, and functional testing, are performed to make sure the product works as intended.
6. Product sterilization
Products typically go through sterilization processes to remove remaining microorganisms so they are safe for medical or pharmaceutical use. Manufacturers commonly use ethylene oxide (EtO) sterilization and gamma irradiation.
How to Select a Clean Room Injection Molding Manufacturer?
Choosing the right clean room injection molding manufacturer makes all the difference in ensuring product safety and quality. Here are some key questions to help you choose:
- Is the manufacturer certified by ISO 14644-1 for cleanrooms or ISO 13485 for medical devices?
- What class of cleanroom does the manufacturer have? Is it suitable for your product?
- Does the manufacturer have experience in producing similar products in your industry?
- Do they have professional injection molding machines to meet your quality standards?
- Do their engineers and technicians have the skills to handle complex projects?
- Do they have rigorous quality control processes in place?
- What will the final part be used for (medical, pharmaceutical or other purposes)?
THY Precision understands the importance of clean room injection molding in delivering safe, sterile, and quality products for the medical, pharmaceutical, and biotechnology industries.
With over 40 years of experience and state-of-the-art facilities, including ISO Class 7 and 8 cleanrooms, we’re able to handle even the most demanding projects. Our commitment to quality and safety is also reflected in our ISO 13485:2016 and ISO 9001:2015 certifications.
Looking for a reliable clean room injection molding partner? Contact us now.