Published on 2024-09-05
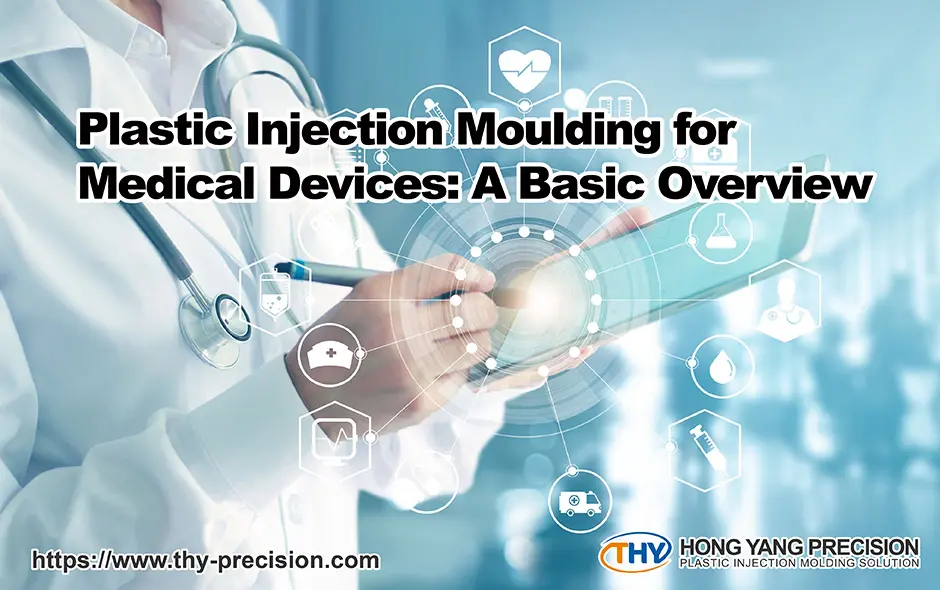
Many medical devices are manufactured through plastic injection moulding, which allows for precise and top-quality components in large-scale production and better aligns with ISO standards. In general, injection moulding for medical devices is conducted in an ISO 8 clean room environment to ensure all products adhere to the strictest standards of sterility and safety.
This article covers how plastic injection moulding is used in the medical industry, focusing on key materials, practical techniques, and the benefits it provides to manufacturers and healthcare providers alike.
Table of Contents
Key Materials Used in Medical Device Plastic Injection Moulding
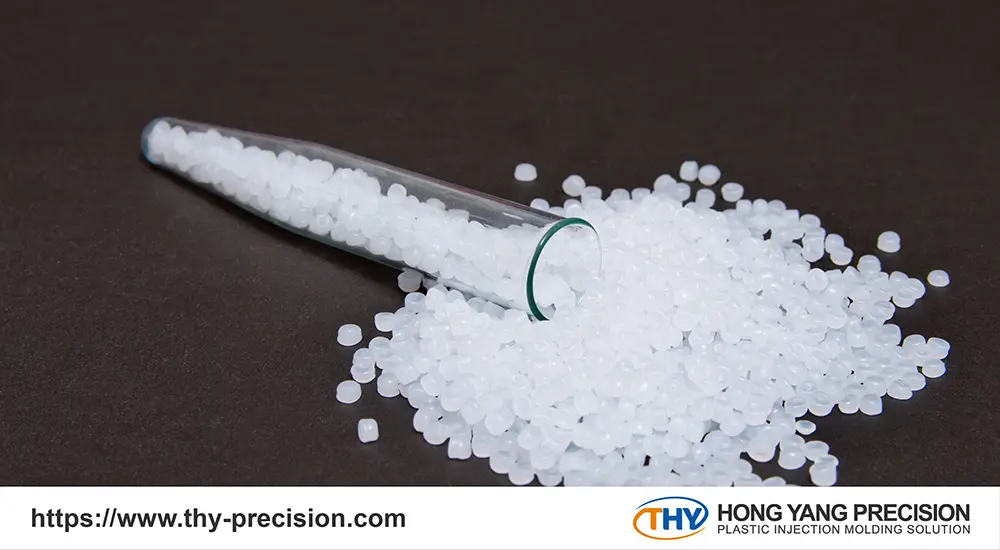
The medical injection moulding process involves heating medical-grade resins until they become moulten. Biocompatibility, toughness, and other mechanical properties should be considered before selecting the resins for injection moulding.
Here is a list of medical-grade plastics utilized in the injection moulding process for creation:
● Polypropylene (PP)
Polypropylene is the most widely used resin in injection moulding, particularly valued for its ability to produce high-precision, size-specific medical components, such as hydrophobic intraocular lens (IOL) discs used in eye disease treatments.
Medical-grade PP enables the efficient mass production of a wide range of devices, including syringes, connectors, and implants. Its strength, impact resistance, and radiation tolerance make it a reliable material for critical healthcare products, offering both effectiveness and cost-efficiency in large-scale manufacturing.
● Polyethylene (PE)
Polyethylene comes in different forms, such as LDPE (Low-Density Polyethylene) and HDPE (High-Density Polyethylene), each with unique properties. LDPE offers greater flexibility due to its lower crystallinity, while HDPE provides higher stiffness and strength.
PE is commonly used in injection moulding to produce durable, biocompatible components like joint prostheses, tubing, and containers. Its lightweight nature and chemical resistance make it suitable for devices that need to withstand sterilization and harsh conditions.
● Polycarbonate (PC)
Polycarbonate is known for its optical clarity and impact resistance, and it is a preferred choice for applications where transparency and toughness are valued. Its ability to serve as a lightweight alternative to glass makes PC particularly suitable for medical devices that require optical clarity and durability.
We’ve discussed the considerations of producing optical lenses in injection moulding.
See our full article here:
The Role of Injection Moulding in Crafting Optical Lenses
Injection Moulding Techniques for Medical Devices
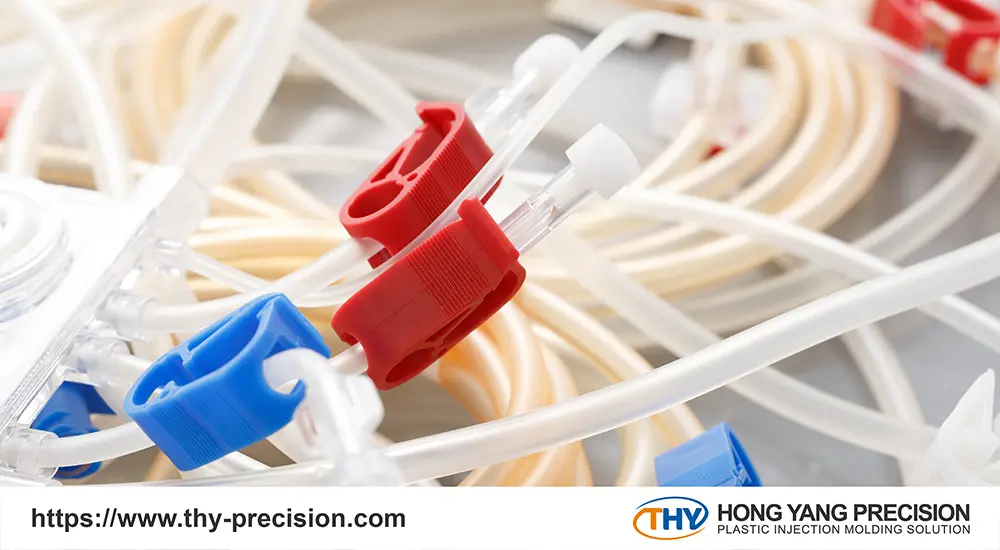
One plastic injection moulding method commonly used in medical devices is Thin Wall Injection Moulding.
Thin wall injection moulding refers to parts with wall thicknesses under 1mm, commonly used in high-volume production for cost efficiency. The process requires higher pressure and faster moulding speeds to prevent the moulten material from freezing and ensure proper cavity filling.
For example, a component with standard walls might take two seconds to mould, but with 25% thinner walls, it may need to be filled in just one second. Careful gate design is essential to facilitate part ejection. This technique is often applied to produce small enclosures for medical devices.
Given the complexity and precision required in such processes, engineers need to maintain strict quality control standards to make sure the final parts perform reliably in medical settings.
IQ, OQ, and PQ: Critical Qualifications in Medical Device Industry
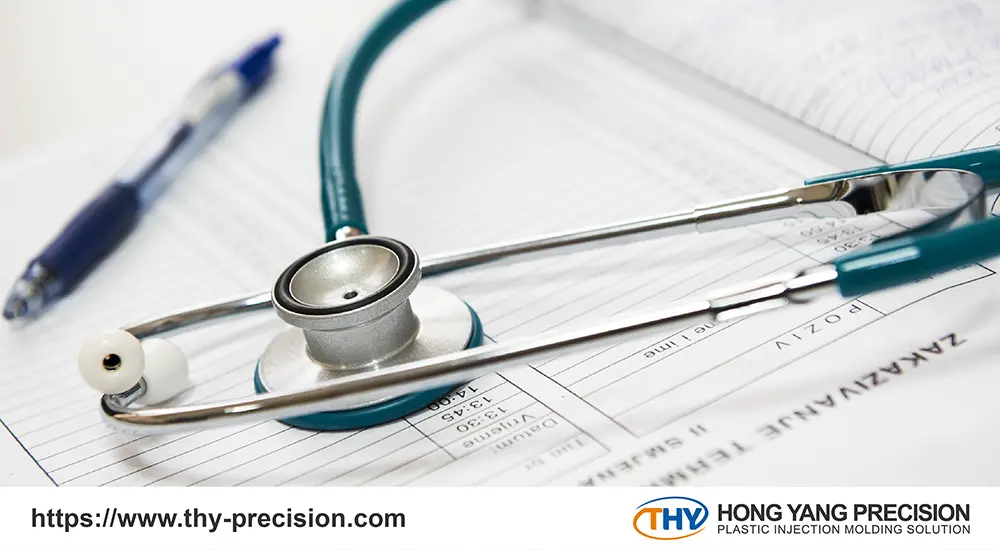
The quality and stability in medical devices are of utmost importance, as even a small defect can have serious implications. In the context of injection moulding, particularly for delicate components like those produced through thin wall injection moulding, rigorous quality assurance (QA) should be implemented at every stage.
Three main stages of validation—Installation Qualification (IQ), Operational Qualification (OQ), and Performance Qualification (PQ) are widely used in the medical device industry. Collectively known as the 3Q process, these stages ensure that the injection moulding process is capable of consistently producing parts that meet the stringent quality standards required for medical devices.
● Installation Qualification (IQ)
IQ ensures that all equipment used in the production, measurement, and testing processes is properly installed, maintained, and calibrated. Documenting the initial installation settings is crucial for identifying the root causes of any process deviations or part instability.
● Operational Qualification (OQ)
OQ verifies that the key performance components of a product or process meet the required specifications. This validation involves setting the appropriate operating limits for various process parameters through analytical methods and engineering studies, ensuring the process can consistently produce parts within acceptable limits.
● Performance Qualification (PQ)
PQ demonstrates that the manufacturing process is stable and capable of producing parts that meet customer expectations. PQ typically involves running the defined process through three separate production runs to simulate actual production conditions and ensure consistent quality.
Benefits of Medical Device Plastic Injection Moulding
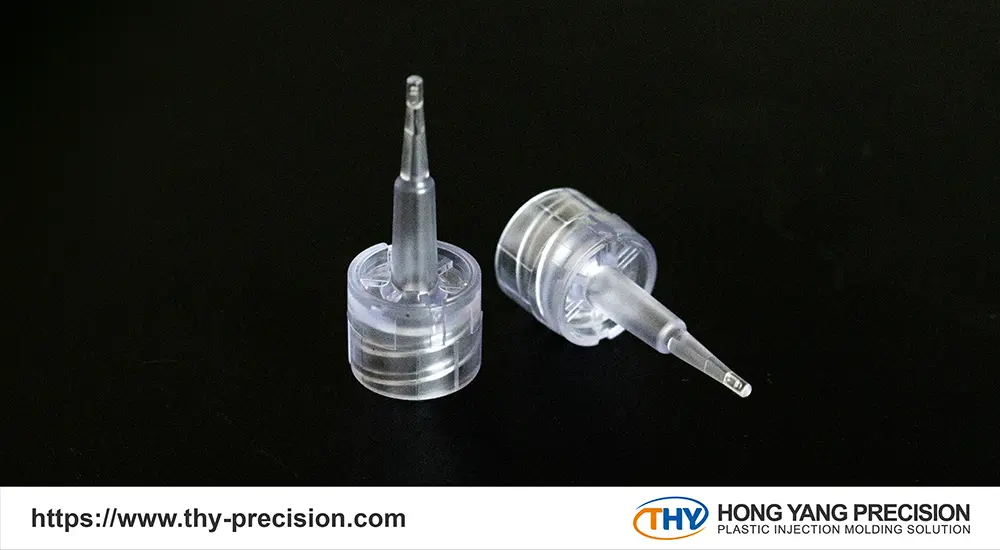
● High Volumes with Low Per-Part Costs
Medical device plastic injection moulding is highly cost-effective, particularly for large production runs. While the initial tooling may be expensive, the cost per part decreases significantly with high-volume production. The automation and precision of the process further reduce labor costs and ensure that each part is produced efficiently.
● Design and Manufacturing Complexity
Injection moulding supports complex designs and precise manufacturing. It allows for the creation of intricate parts with tight tolerances(±0.1mm is the typical range) and high accuracy up to ±0.005mm. This advantage is significant for medical devices where even minor deviations can affect performance and safety.
● Wide Selection of Medical Materials
The injection moulding process accommodates a diverse range of medical-grade materials, offering flexibility to meet various industry standards and requirements. This extensive material selection includes PP, PE, PC, and silicones that provide the necessary strength, durability, and biocompatibility for different medical applications.
Choosing the Right Partner for Medical Injection Moulding
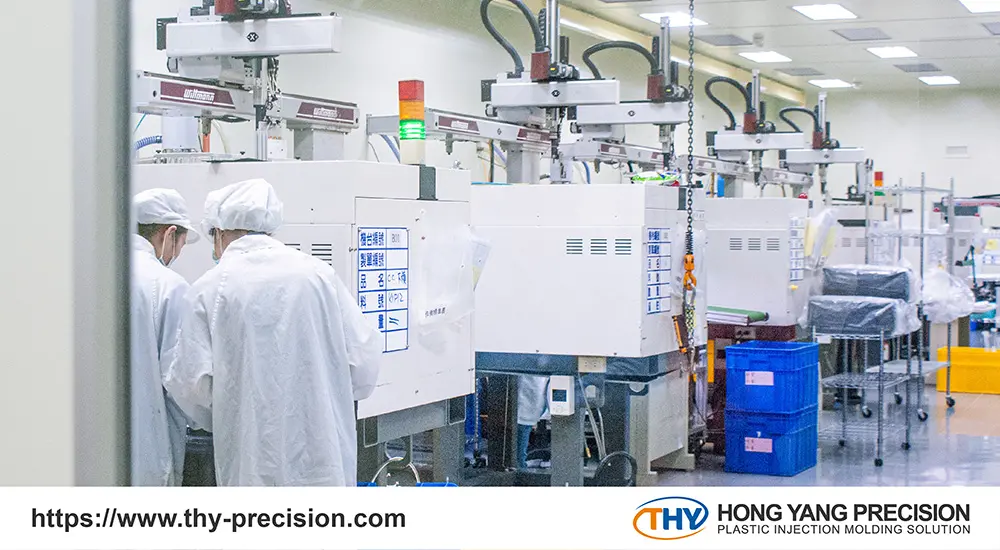
When selecting the right partner for medical device plastic injection moulding, here are key questions to evaluate:
- How long has the company been involved in medical injection moulding?
- What types of medical devices have they successfully manufactured before?
- Is the company familiar with FDA regulations and ISO standards for medical device production?
- Do they have experience with certifications such as ISO Class 7 and Class 8 cleanroom environments?
- What types of injection moulding machines and technologies do they use?
- Do they offer real-time monitoring and quality control?
At THY Precision, our skilled engineers are ready to assist you in refining your design and choosing the right materials for your components.
We operate over 80 high-capacity machines, ranging from 30-ton to 300-ton presses, and are able to produce millions of units each month with real-time quality monitoring. Our facility includes an ISO Class 8 cleanroom for moulding and an ISO Class 7 cleanroom for assembly, building the sterile and contaminant-free environment for production and packaging.
Some medical devices require sterilization services; THY Precision also provides EO (Ethylene Oxide) and Gamma sterilization to help protect millions of patients from the risks of infectious diseases caused by bacteria, viruses, and fungi.
We are experienced in producing a variety of Class II and Class III medical devices, including:
- Medical Filtration and Implantable Components: Chamber Filters, Dialyzer Filters, etc.
- Intravenous and Infusion Components: Pump Connectors, Intravenous Infusion Drip Components, Bacteria Filter, etc.
- Medical and Laboratory Consumables: Plastic Components for Blood Bags, Beakers, Petri Dishes, Containers in Laboratory, and Injectors for intraocular lens (IOL) applications, etc.
For more information on how we can assist with your project, please contact us to discuss your specific needs and explore how THY Precision can support your medical device plastic injection moulding requirements.